002 Welding: Distortion and how to deal with it
1. Distortion due to welding
Welding is an excellent processing method for joining parts together, but distortion may occur due to the process.
This time, we will introduce this trend and how to deal with it.
During the welding process, the area around the weld becomes high temperature, and when it returns to room temperature, it shrinks, causing distortion at the center of the weld.
Distortion becomes especially large when the base metal is thin, when the weld penetration is deep, when the leg length is long, or when welding is performed only from one side.
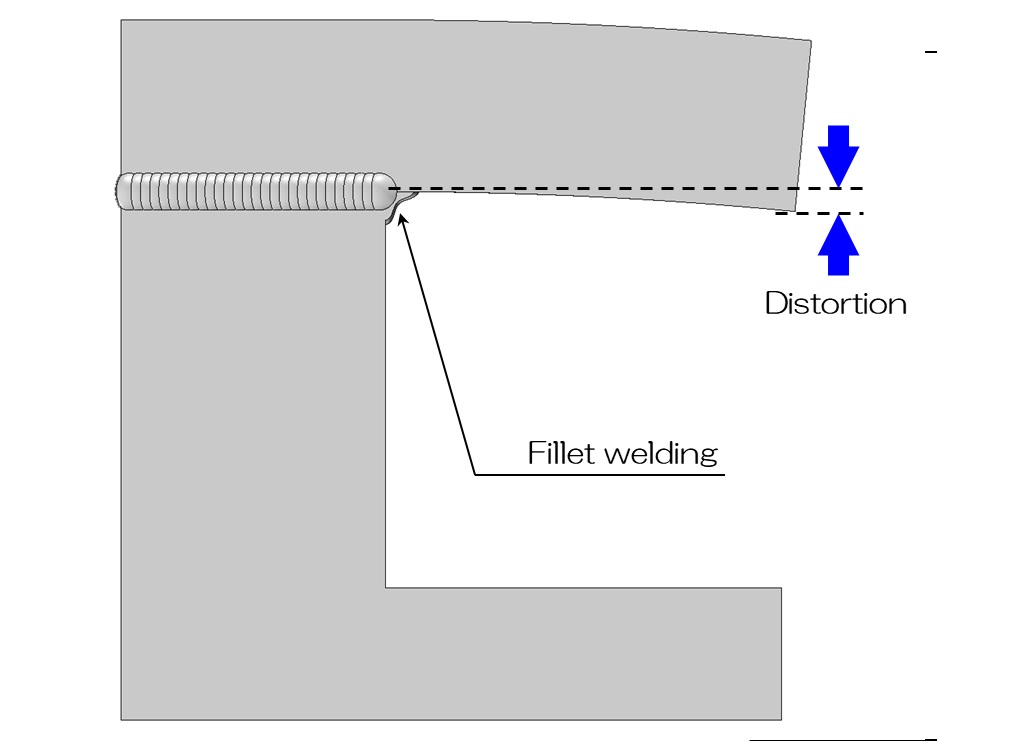
In the example shown above, the part protruding from the fillet weld is deformed as if bowing starting from the weld.
If this type of distortion caused by welding is unacceptable, the following measures can be taken.
(1) Correct after welding
(2) Perform secondary processing after welding
(3) Change welding locations and instructions
(4) Change the design
2. Correction after welding
Distortion caused by welding can be corrected by applying external pressure with a press or by hitting it with a hammer.
However, since force is applied from the outside, there is a possibility that marks may remain on the contact area, and distortion cannot be completely removed.
In some cases, the side opposite to the welding surface is seared or corrective welding is performed.
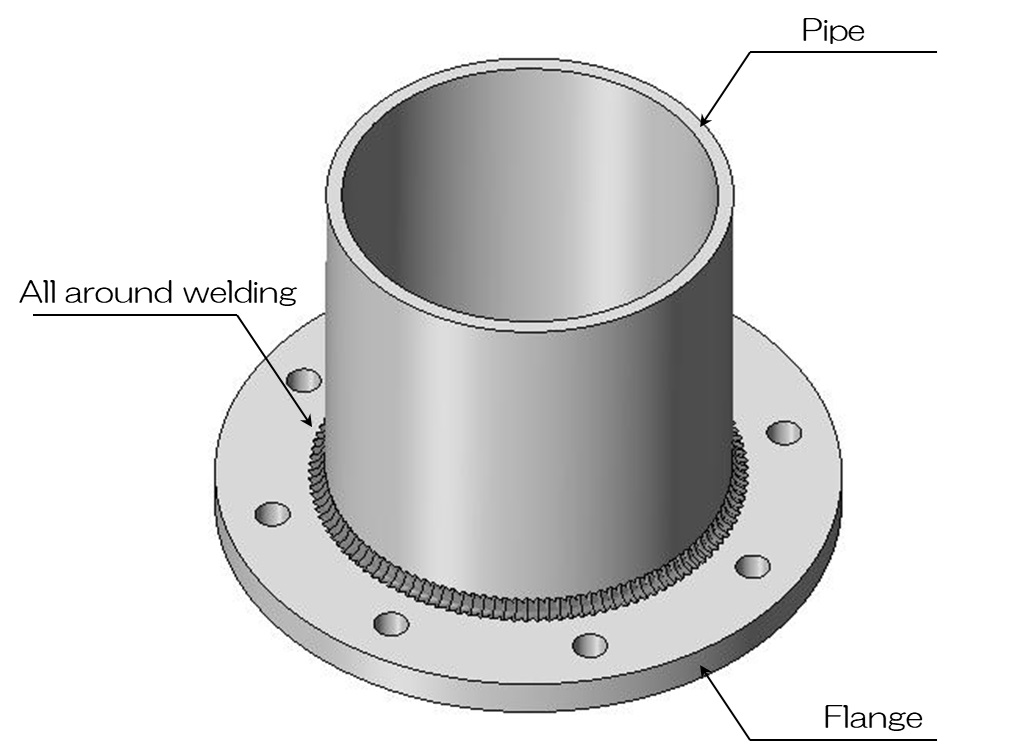
For example, a typical case is welding a flange to a pipe as shown in the diagram above.
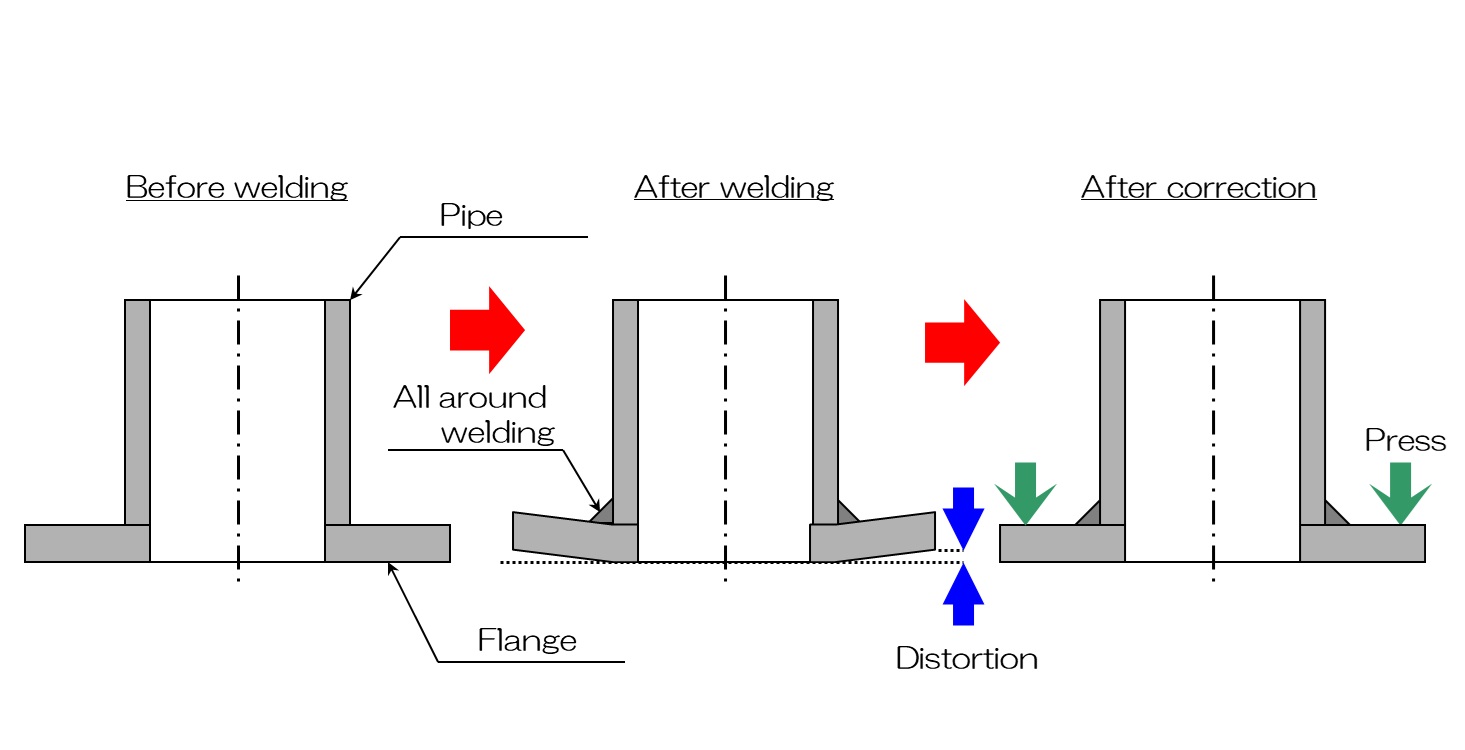
In such cases, it is common to apply pressure to the flange surface to correct it.
Additionally, welding on the outer diameter side increases distortion, so welding on the inner diameter side to reduce distortion can also be said to be an effective countermeasure.
3. Secondary processing after welding
For example, if flatness of the contact surface is required, such as on the flange surface of piping, it may be possible to ensure machining accuracy by performing secondary processing such as cutting after welding.
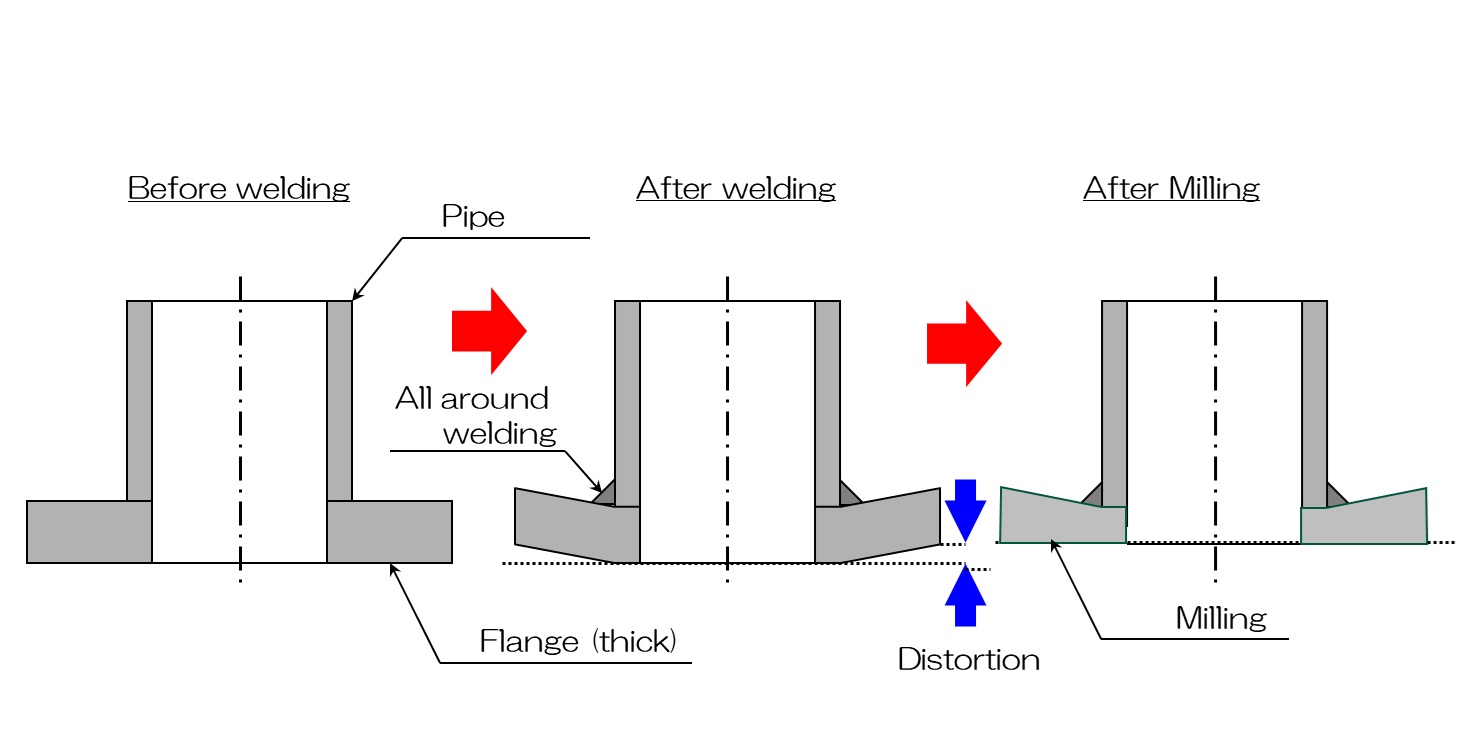
Of course, the board thickness before secondary processing must be thicker than the finished dimensions to account for distortion.
Be sure to keep in mind the thickness of the material standard before specifying the finished dimensions.
For example, the standard thickness of stainless steel flat bars is t10mm, t12mm, t16mm, and t19mm.
If the finished dimension is t10mm, you will need to use t12mm or t16mm material.
If you perform secondary processing only in areas where precision is required, and allow for distortion in areas where it is not needed, you will end up with a rational design.
4. Changes in welding locations and instructions
Particularly when the plate is thin, distortion will increase if weld the entire circumference.
It is best to avoid full-circumference welding, unless steps or gaps cannot be tolerated in joints such as sanitary piping, food/medical-related applications, or cases where strength cannot be ensured without full-circumference welding.
If you are not particular about it, it would be a good idea to instruct in a note to basically use so-called tap welding (intermittent fillet welding).
Alternatively, it is also effective to change the design to avoid welding near areas where deformation is not desired, and to weld in areas where distortion is less likely to occur.
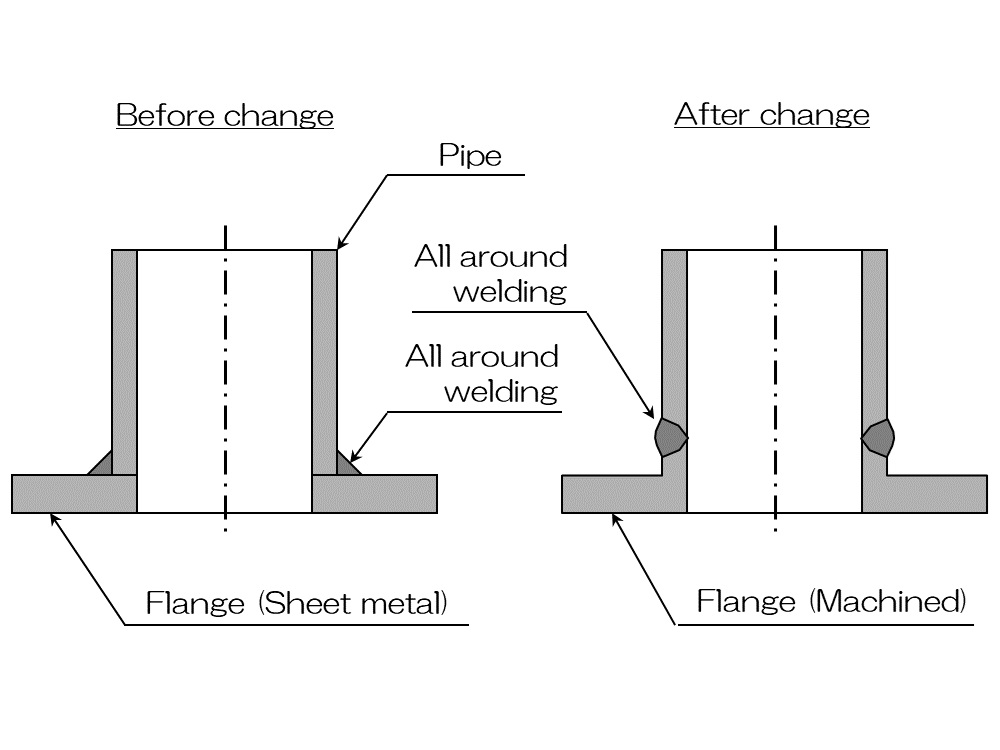
For example, as shown in the diagram above, it is possible to eliminate distortion on the flange surface by making changes such as butt welding on the pipe side instead of welding at the base of the flange.
However, the flange is not made from sheet metal, but instead made using a lathe.
There is a trade-off between the high cost of parts and the high cost of straightening and secondary processing after welding, so it is necessary to carefully consider the required accuracy.
Please consult with the manufacturing site.
If you carelessly specify a value that is too large for the leg length, it may cause unexpected distortion.
It is safe to set the value as small as possible within the allowable range, but if you are not particular about it, you can also leave it up to the manufacturing site.
Skilled craftsmen determine the appropriate welding pitch and leg length based on the shape and other factors.
While communicating easily with the manufacturing site, try to give more rational welding instructions.
5. Change the design
Welding is a rational method for joining different parts to create complex shapes.
On the other hand, there are also aspects such as deformation caused by welding and inferior strength compared to one-piece processing, so it may not necessarily be rational depending on the content.
In some cases, changing the design, including the shape, may be an option, such as cutting it out or dividing it.
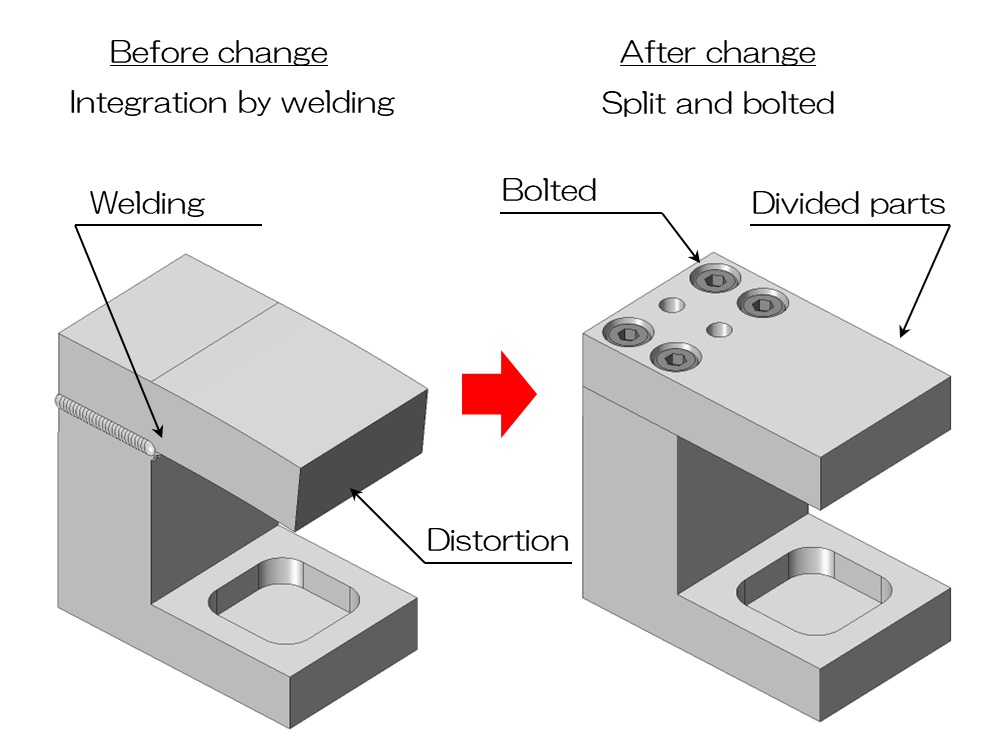
Distortion is inherent in the welding process, so it would be a good idea to consider the effects and countermeasures when designing rationally.
Please feel free to exchange information with the manufacturing site.