017 Milling: Undercut that are difficult for milling
1. What shapes are difficult for milling?
Milling is an important processing method in the production of mechanical parts.
By cutting away unnecessary parts, highly accurate machining and various shapes can be achieved.
Although it is a highly versatile cutting process, there are actually some shapes that it is not good at.
A typical example is a shape called an undercut.
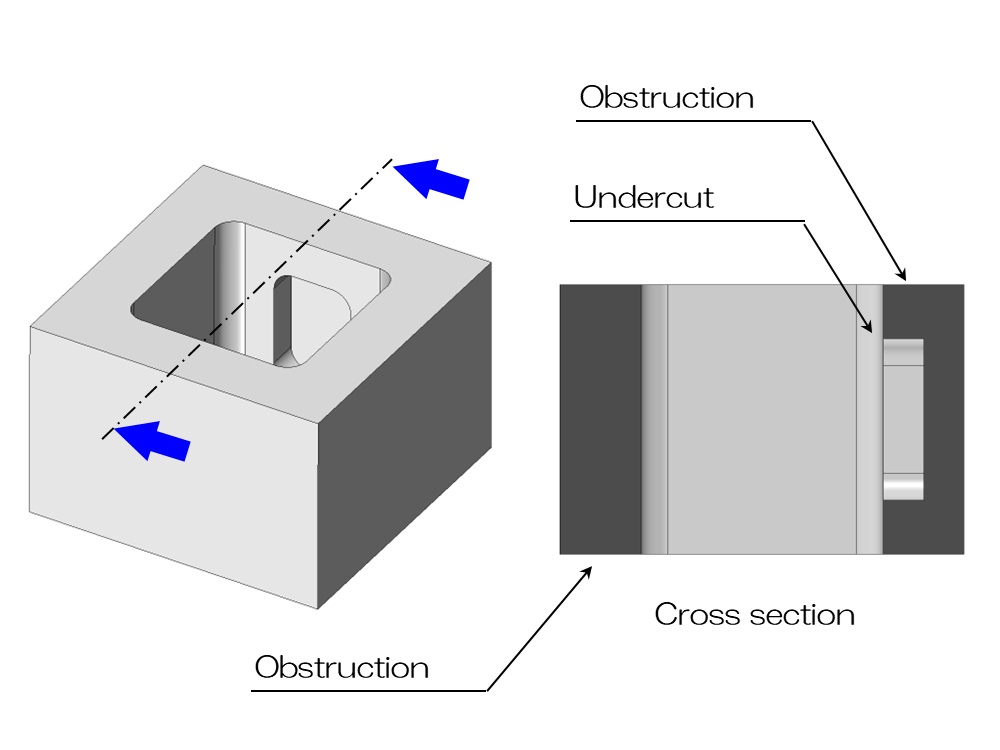
A typical example of an undercut is the shape shown above.
Undercut is a term originally used for molded products.
Refers to a shape that enters from the side that obstructs the opening and closing direction of the mold.
In machining, an undercut is a shape that extends sideways to the end mill's approach direction and cannot be machined.
There is no problem with dents on the outside, but dents on the inside, as shown in the image above, are a big problem.
With a shape like this, the front wall gets in the way, so even if you try to cut it with an end mill, you won't be able to cut it.
2. Example of undercut processing
If there is an undercut shape on the inner surface, it is difficult to process it by cutting alone.
In such cases, die-sinking electrical discharge machining is often used.
Die-sinker electric discharge machining is a processing method often used for manufacturing molds.
It is also used to remove the corner radius that inevitably occurs during cutting to create pin angles.
Attach an electrode with an inverted shape to the die-sinking electrical discharge machine and bring it close to the material while energizing it.
Then, a discharge phenomenon occurs between the electrode and the material, melting the material and making it possible to transfer the shape of the electrode.
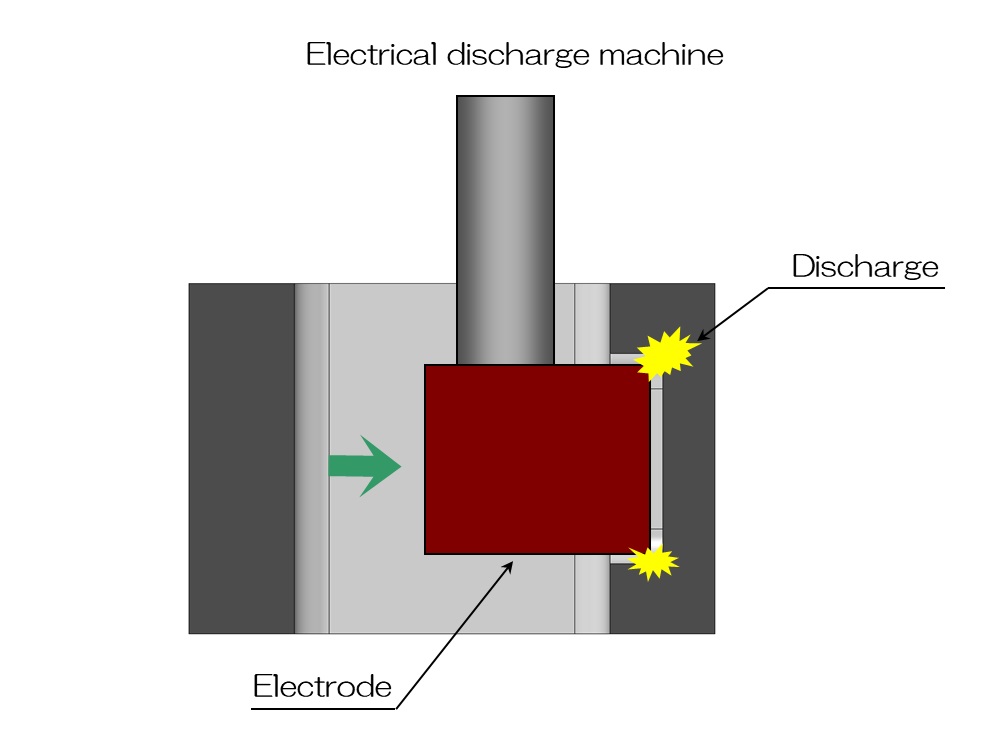
To perform die-sinking electrical discharge machining, an electrode that is the inverted shape of the desired shape is manufactured by cutting.
Die-sinking electric discharge machining is not a speedy process that physically scrapes away the material like cutting, but it is a process that slowly and gradually melts the material, which takes longer processing time.
In other words, this method requires more processing fees and construction time.
In addition to die-sinking electrical discharge machining, the following methods can be considered for forming undercuts.
The first method is to attach an attachment called an angle head that allows the main axis of cutting to be tilted 90 degrees.
However, since the angle head itself is of a certain size and the end mill is long, it cannot be used unless a case with sufficient machining space is available.
The second method is to penetrate the undercut part from the outside, process it, and finish by welding parts that fit there.
Naturally, welding causes distortion, so if processing precision is required, secondary processing after welding is required.
The third method is to create the material using a 3D printer or lost wax instead of cutting it from a block, and perform secondary processing only on the parts that require precision.
3D printers are becoming more common, but metal is still expensive.
If the shape is complex, the deformation will be large.
In any case, parts with undercut shapes cannot be manufactured easily.
If it is absolutely necessary, there are processing methods such as those mentioned above, but all of them take time and cost.
It is safer to design a design that does not require undercuts as much as possible.
In the next article, we will introduce how to avoid undercuts due to design changes.