009 Milling: Working surface and setup change
1. What is a working surface?
In milling, processing is performed on the surface directly facing the direction of the end mill (spindle).
You can perform various removal processes such as cutting the outline, digging pockets, cutting steps, and drilling holes.
This time, we will explain the relationship between this working surface and setup changes.
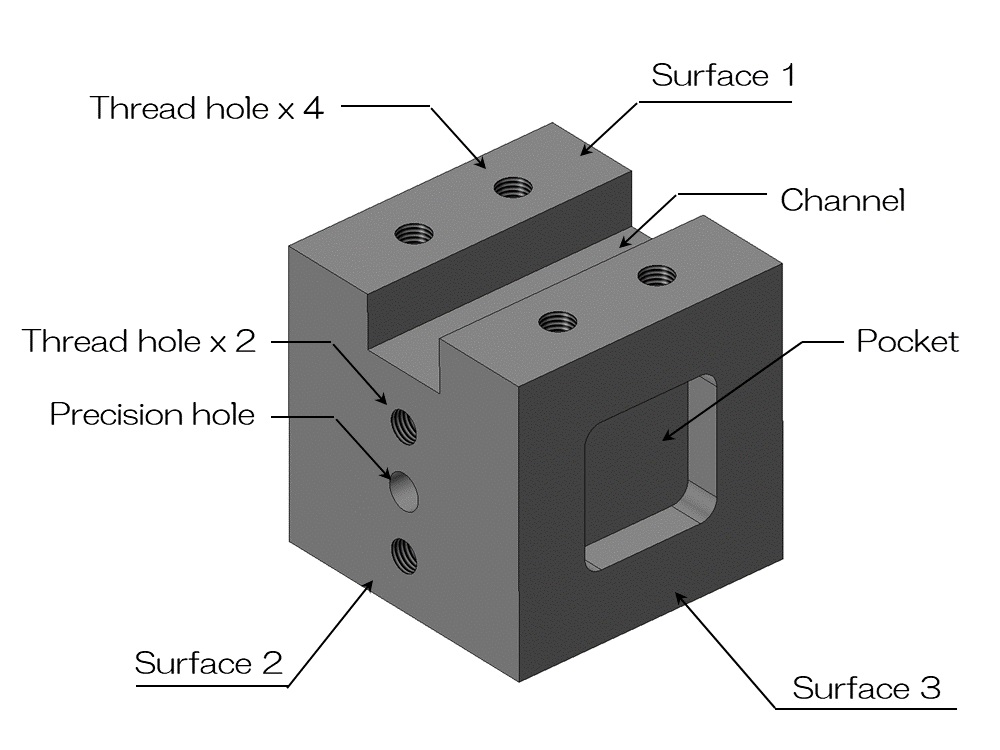
Let's imagine a block like the one shown above.
The basic cutting parts are block-shaped hexahedrons like this one.
This block has a regular hexahedron with processing applied to each of the three sides shown.
Side 1 has 4 grooves and screw holes, side 2 has a reamed hole and 2 screw holes, and side 3 has a pocket shape.
2. Surface 1 processing
First, let's assume that we will be machining surface 1 of this block.
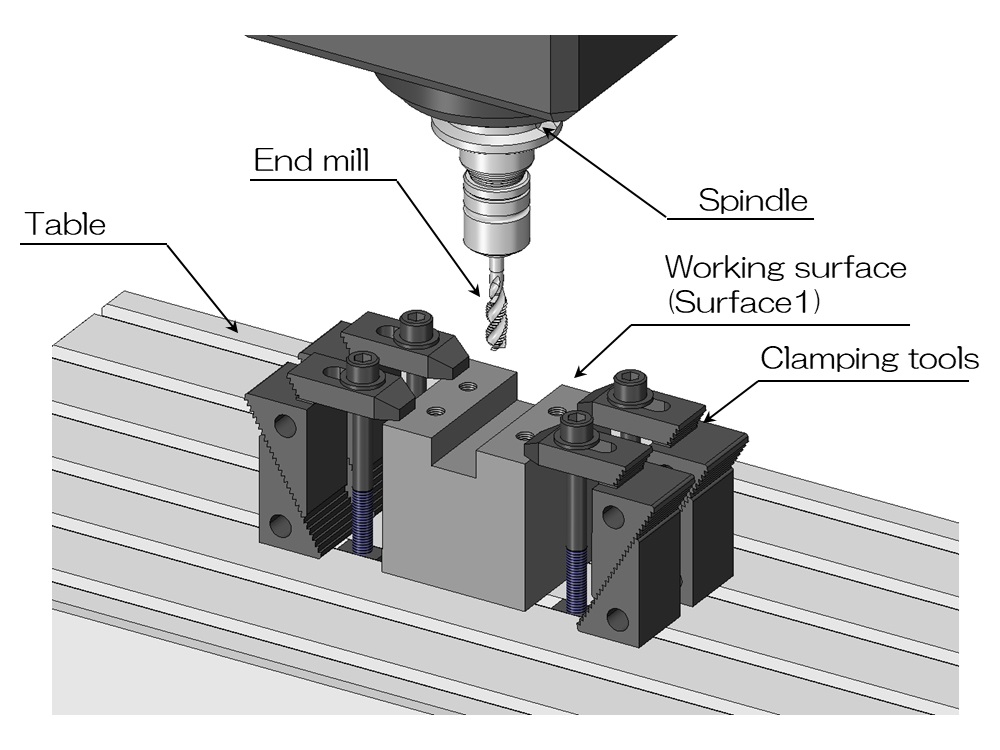
First, fix the material on the table surface with the processed side facing up.
After that, set the tools, create an NC program, and perform the machining.
The figure above shows the state when surface 1 processing is completed.
The preparatory work before actually cutting the material is also called setup work.
The setup work will be explained in detail in another article.
Now, I want to process surface 2 next, but I can't process it as is.
When viewed from the spindle, the area that becomes surface 2 is an undercut that cannot be machined.
To process side 2, you must unfasten the material, turn the material over, and perform setup work again.
The process of undoing such a setup and starting the setup again with a new machining state is called a setup change.
3. Surface 2 processing
Process it with side 2 facing up as shown in the figure below.
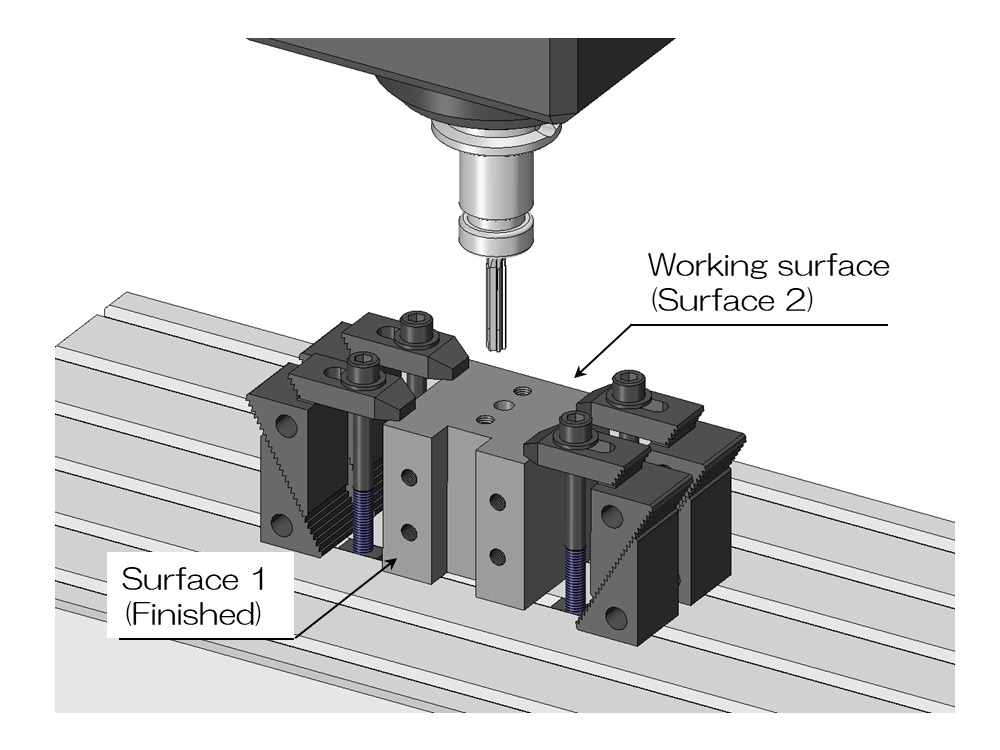
The above figure shows the state after the setup has been changed and surface 2 has been machined.
4. Surface 3 processing
Once the machining of surface 2 is completed, we will change the setup and proceed with the machining of surface 3.
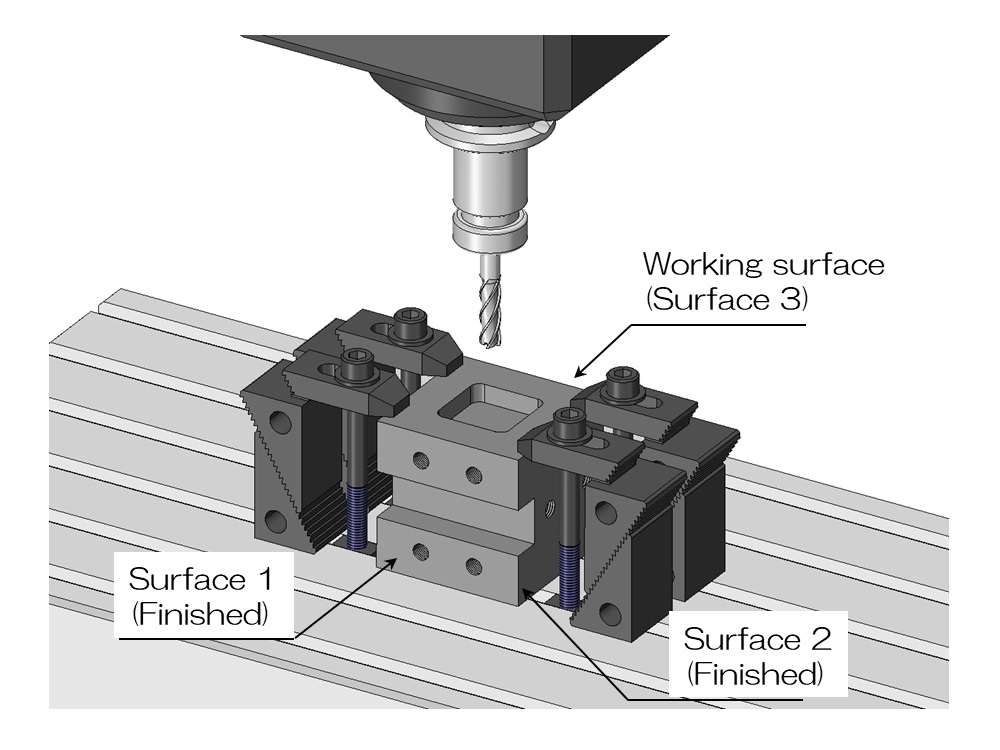
The above figure shows the state in which surface 3 has been machined.
Having made it this far, the product is finally complete.
In this way, in milling-based cutting, machining is performed one side at a time while changing setups so that the machined surface faces upward.
Naturally, as the number of surfaces to be machined increases, the number of setup changes will increase.
Setup changes include a lot of analog work by workers.
As the number of setup changes increases, the number of machining steps increases, which increases machining costs, and also causes deterioration of machining accuracy.
On the other hand, if the number of setup changes is reduced, costs will be reduced accordingly.
If you take measures such as aligning the size and direction of the radius or standardizing the holes, the number of setup steps will be reduced accordingly.
Additionally, by using 5-axis machining, setup changes may be omitted.
We will explain 5-axis machining in another article.