018 Milling: Avoiding undercut by design change
1. Undercut issues
In machining, machining an undercut shape that cannot be approached with an end mill from any direction is one of the difficult shapes to realize.
In some cases, it may be possible to process the material through the manufacturer's ingenuity, such as die-sinking electric discharge machining, using an angle head, or combining it with welding.
Another option is to create the material using a 3D printer or casting, and then finish the necessary parts using cutting.
However, all of these methods can significantly increase cost and construction time.
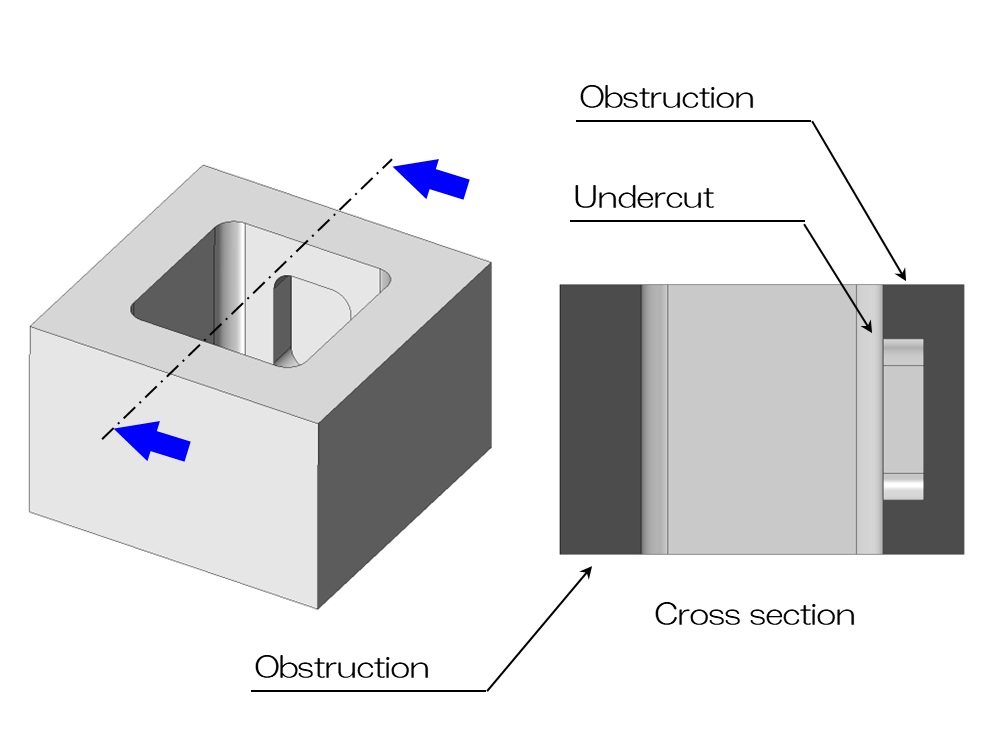
After all, it is most rational for the design side to devise a shape that can be easily processed at the manufacturing site.
This time, we will introduce a method to avoid undercut shapes by changing the design.
2. Not create undercuts
Is the shape of the undercut necessary in the first place?
I think it would be a good idea to first consider designing a similar shape that does not result in undercuts, as shown below.
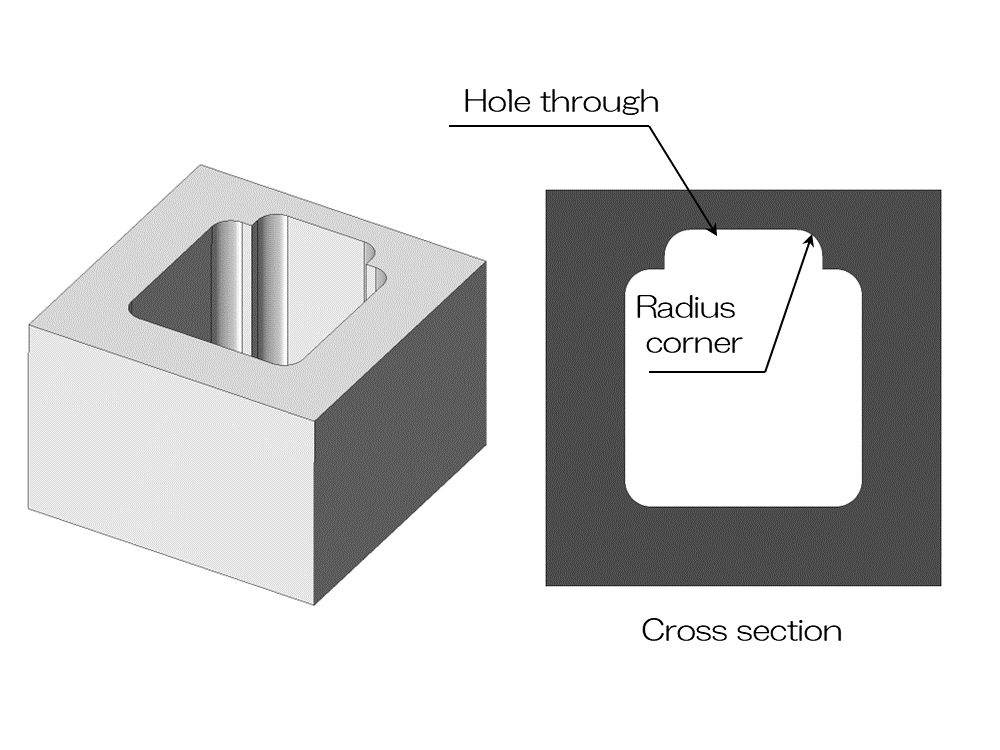
The above figure is an example of a modification in which the undercut section is dug in the vertical direction.
For cutting, it is necessary to add a rounded shape to the inside.
If the radius is unacceptable, wire electrical discharge machining can be used instead of cutting.
This is an example where the options for processing methods increase as long as the material is penetrated.
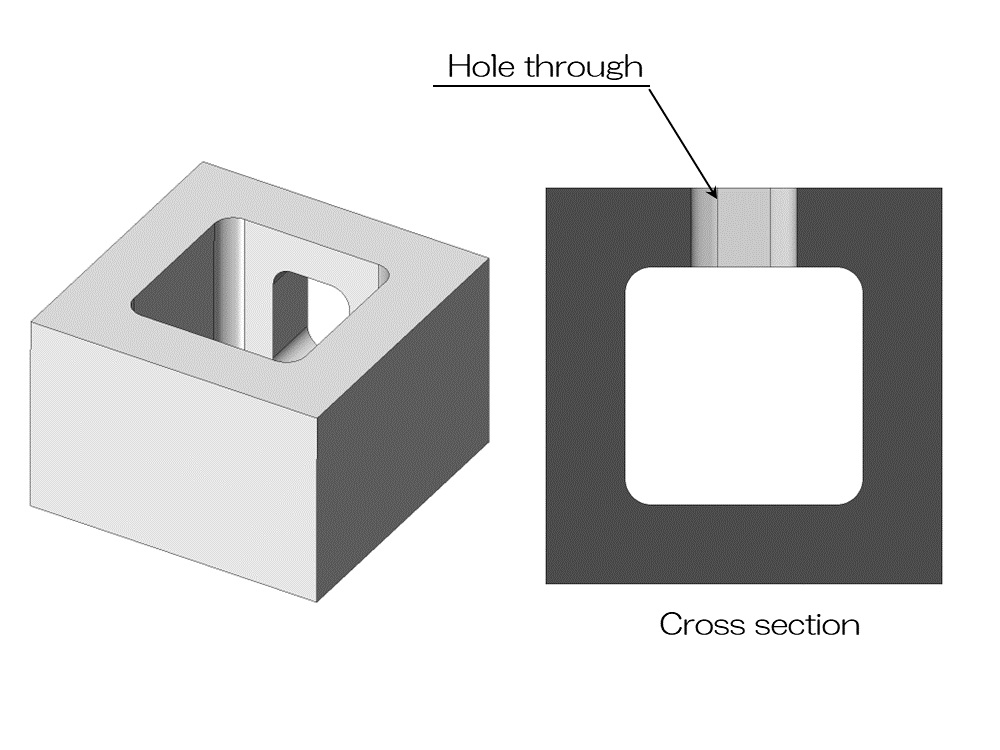
The above figure is an example of a modification in which the recess in the undercut section is passed through to the back.
If there is no need for it to stop in the first place, the basic rational design for cutting is to make it penetrate.
In this way, it is also possible to process from the back side.
You could also consider cutting it through, then closing it off from the back and welding it in.
3. Undercut shapes that can be processed
For example, there are blades called side cutters and T-slot cutters.
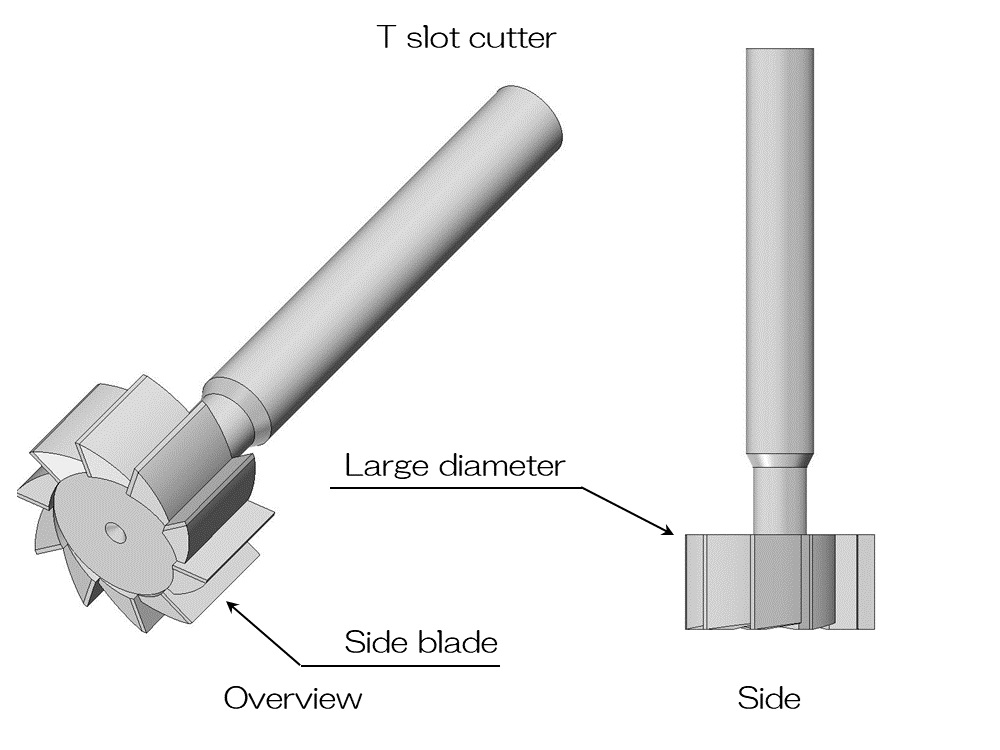
For example, a T-slot cutter has a large diameter blade that faces sideways, as shown in the image above.
It can be mainly used to cut T-shaped grooves called T-slots and to form undercuts like this.
If the shape of the undercut can be changed to match the shape of a blade such as a T-slot cutter, it may be possible to process it by cutting.
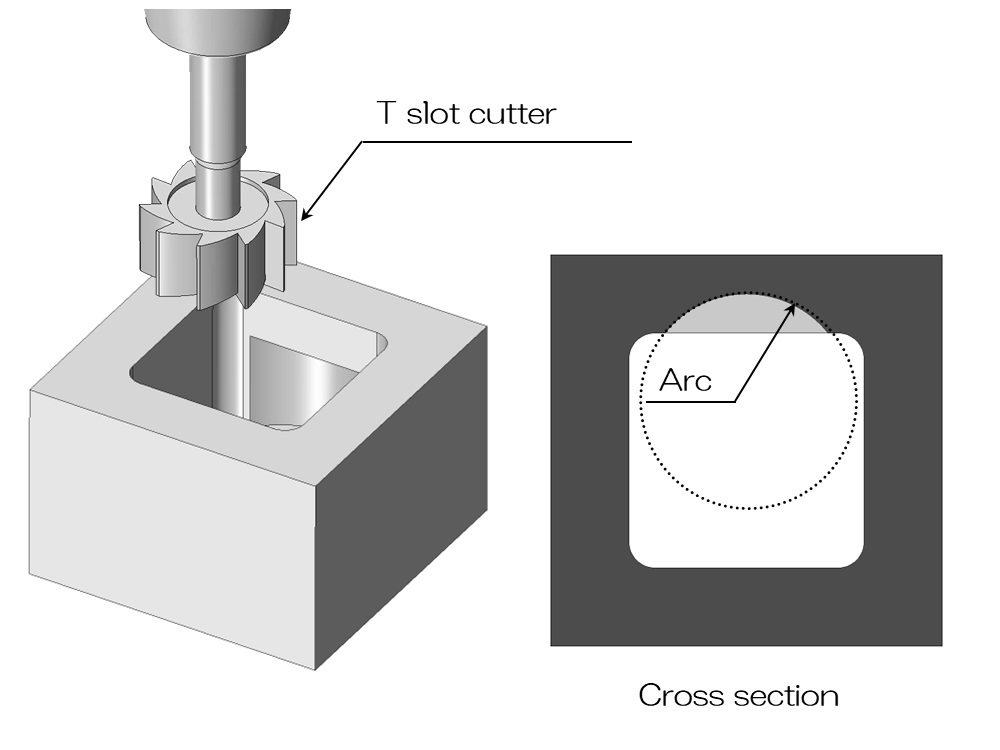
4. Adding shapes for processing
The end mill cannot approach the undercut area, so it cannot be machined.
Therefore, one option is to intentionally add a shape for processing, even though it is not necessary for the purpose of the part.
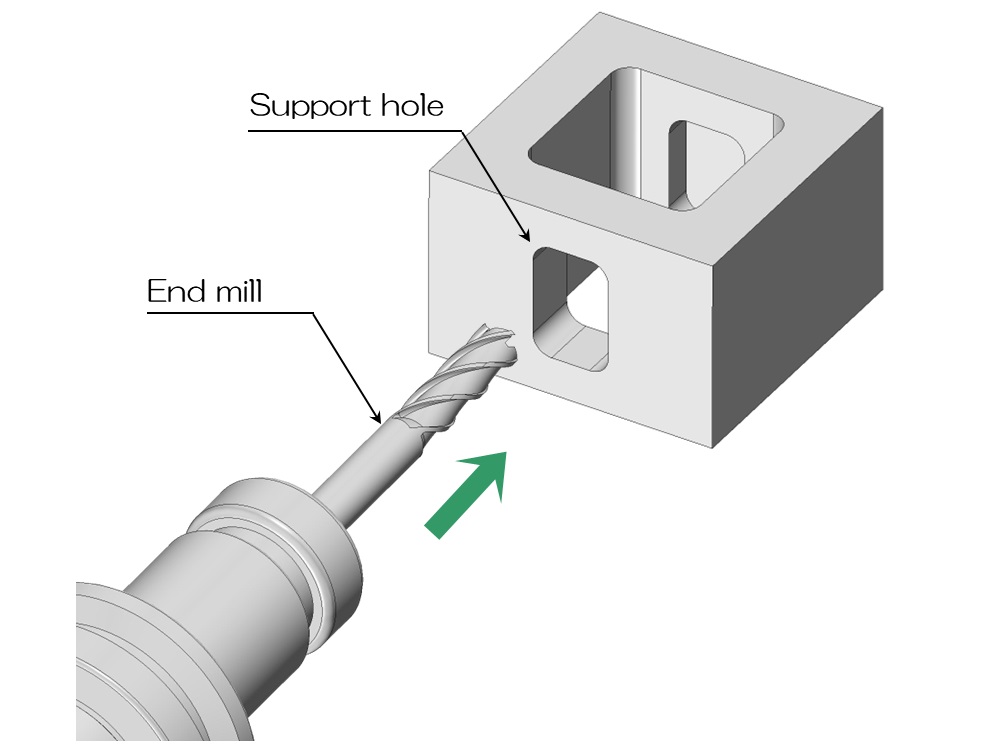
For example, what if you dare to make a hole in the wall in front of you for machining, as shown in the diagram above?
You can approach the end mill through that hole and dig into the undercut.
Of course, settings must be made taking into account the relationship L/D ≦ 5 between the protrusion amount and diameter of the blade.
Please keep in mind that adding such a shape for machining will make machining easier.
5. Separation
If you really need the shape of the undercut part, one way is to separate the parts.
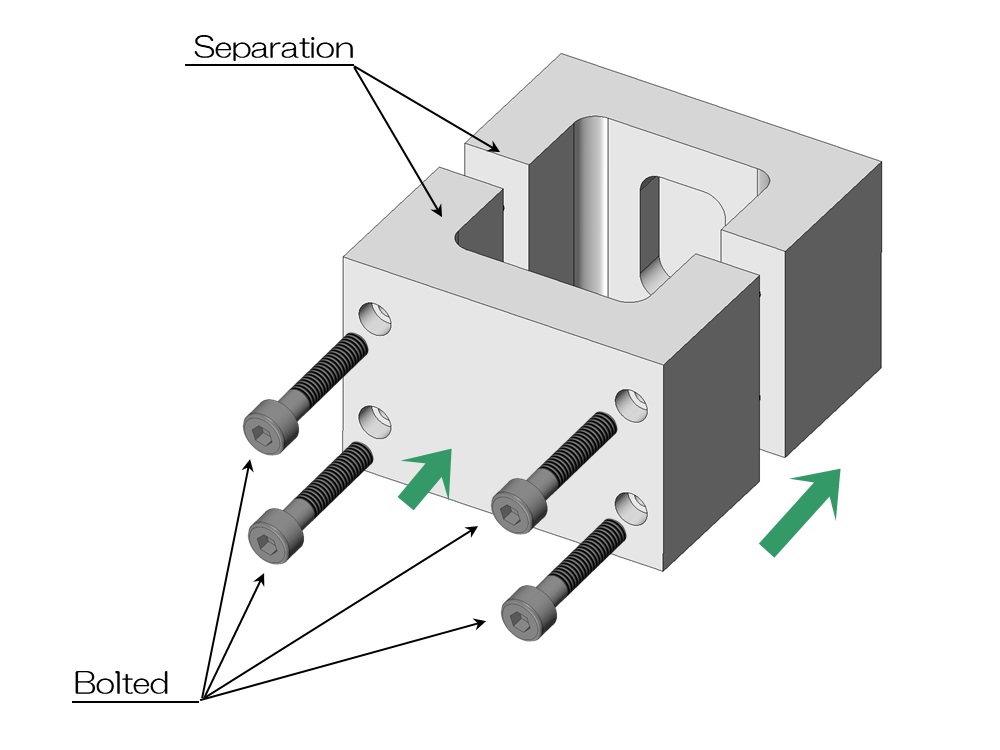
As shown in the diagram above, by dividing the parts and fastening them with bolts, machining of the undercut becomes easier.
Although the number of parts will increase, there is a great possibility that the total cost will decrease.
One way to streamline the process is to simply divide the parts without forcing the shape into a single part.
There are many ways to make things easier at the manufacturing site, but the most effective way is to make things easier to process on the design side.
Please take a look at the method introduced here.