008 Milling: Types and features of milling machines
1. Features of milling process
Milling is a processing method in which the material is set on a machine such as a machining center or milling machine, and the material is cut while rotating a tool (end mill) to create the required shape.
This method of cutting a fixed material using a rotating end mill is called milling.
Due to its principle, milling often produces block-shaped hexahedral parts.
Conversely, general machined parts are based on a hexahedral shape that is intended for milling.
On the other hand, turning a round material at high speed and cutting it with a cutting tool is called lathe processing.
Lathe processing is sometimes called turning.
Parts intended for lathe processing, such as shafts and pipes, are basically cylindrical.
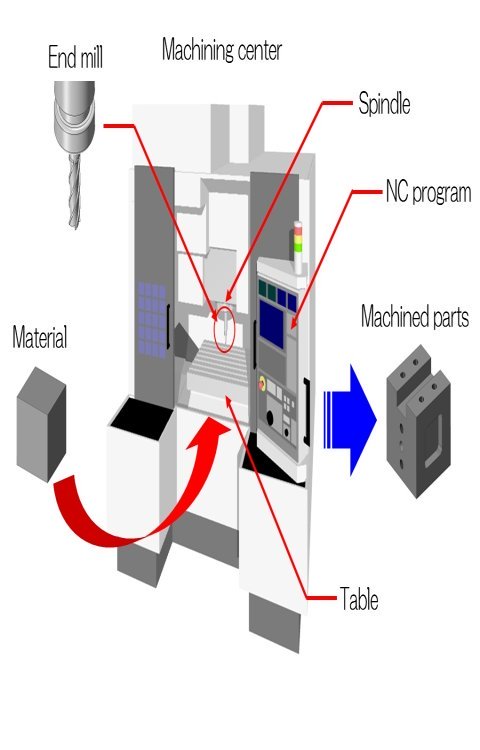
In recent years, so-called machining centers like the one shown above are often used.
In milling, it is important to control the relative positional relationship between the end mill and the material.
Generally, the left and right direction toward the machine is called the X axis, the front and back direction is called the Y axis, and the vertical direction is called the Z axis (for vertical machines).
The axis directions in which the spindle and table move vary depending on the structure of the machine.
There are structures in which the spindle moves only in the Z direction and the table moves in the X and Y directions, and there are also structures in which the spindle moves only in the X and Z directions and the table only in the Y direction.
These differences in structure affect the rigidity, size, processing accuracy, etc. of the machine.
2. Types of milling machine
Milling machines are equipped with a mechanism that sets and rotates an end mill called a spindle, and this spindle and the table surface on which the material is set move relative to each other back and forth, left and right, and up and down.
Milling-type cutting machines are classified based on how the table and spindle are moved, and how the end mill is replaced.
Type | Drive | Tool change |
---|---|---|
Analogue milling machine | Manual | Manual |
NC milling machine | NC controlled | Manual |
Machining center | NC controlled | Automatic |
Analogue milling is operated by a craftsman who rotates the handle, so the accuracy of the workmanship tends to be influenced by the skill level of the craftsman.
Although it is not suitable for complex shapes or mass production, it can be used for processing that is difficult to handle with machining centers, such as secondary processing of castings.
NC milling cutters operate automatically according to a program called an NC program.
Although it can handle products with complex shapes and high precision, tool changes must be done manually, so tools must be changed manually each time the type of machining changes.
Each time, machining stops and tools need to be replaced.
A machining center is a system that automates even this tool change.
A mechanism for automatic tool change called ATC (Automatic Tool Changer) has been added.
If you set the necessary tools in advance, you can continue machining without stopping while automatically changing tools.
It is a cutting machine with advanced automation.
As mentioned above, each processing machine has its own characteristics, so the relationship is not upward compatible in the order of general-purpose milling machine → NC milling machine → machining center.
On the other hand, while the technology for complex and precise machining using machining centers has progressed and it is becoming possible for anyone to handle it, the number of experienced general-purpose millers is rapidly decreasing.
There are many processed products that cannot be realized without general-purpose milling, so machining skills using general-purpose milling are now extremely valuable.
4. Difference between vertical and horizontal
The above diagram shows a typical vertical machining center, but horizontal machining centers with the main axis facing laterally are also widely used.
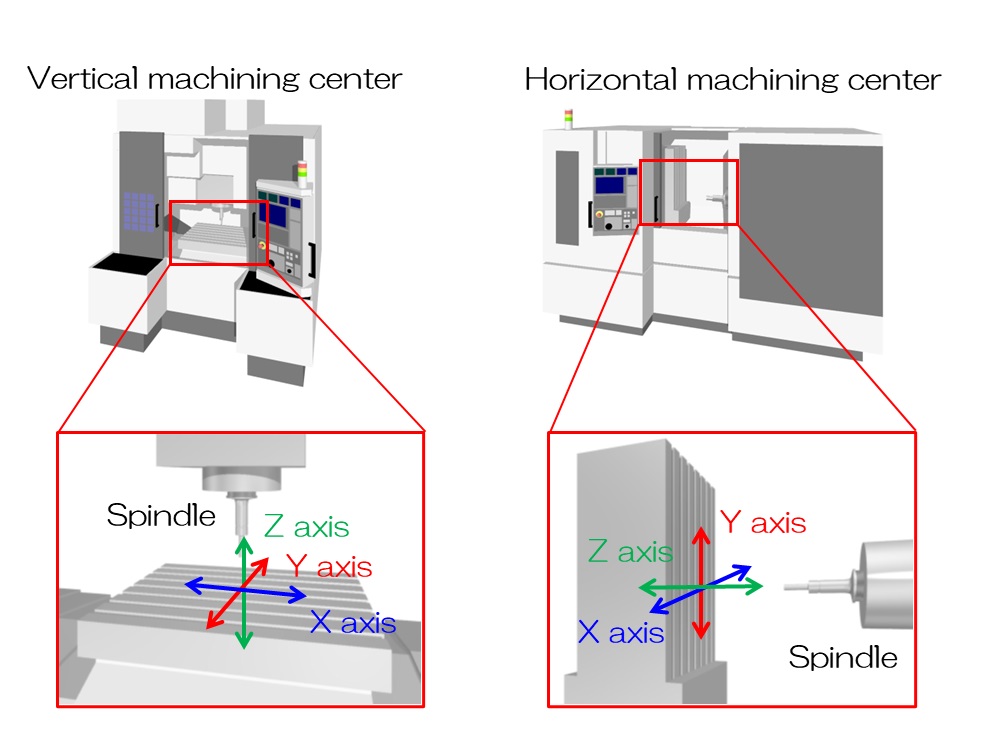
There are differences between vertical and horizontal types as shown in the diagram above.
In a horizontal machining center, the spindle is oriented horizontally, and a table is installed opposite the spindle.
For this reason, it is easy to remove the scraps (called chips) that have been scraped off, and they are less likely to accumulate around the material.
If chips accumulate, they may get caught between the material and the end mill, causing a negative impact on the product without you noticing.
Since the main axis of a vertical machining center moves vertically, it requires space in the height direction including the movable parts, but it requires less space in the lateral direction.
On the other hand, horizontal machining centers require more horizontal space.
Horizontal machining centers are shaped like a raised table, as shown in the diagram above.
Also called tombstones, many of them can be rotated 180 degrees.
In this case, it is often possible to fix the material on the opposite side of the machined surface, allowing continuous processing on both the front and back sides.
In terms of cost, they tend to be more expensive than vertical types.
5. 3 axis and 5 axis
What we have described so far is a processing machine that operates in the three axes of X, Y, and Z.
A machine capable of machining on three straight axes is also called a 3-axis machining machine.
In addition, there are cutting machines that can change the material and the angle of the spindle.
A machine that can change the angle in one direction is called a 4-axis machine, and a machine that can change the angle in two directions is called a 5-axis machine.
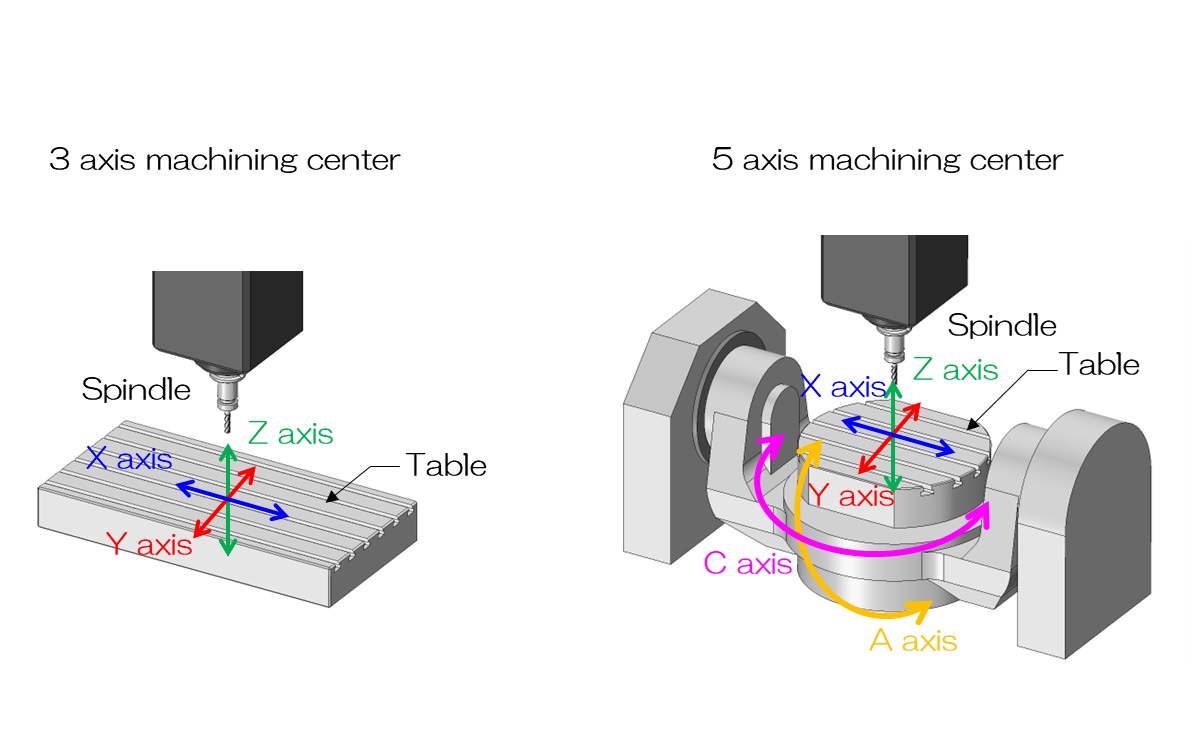
It has advantages such as being able to process more complex shapes and eliminating setup changes, but it reduces the rigidity of the machine and is not suitable for heavy cutting, the machine tends to be complicated and expensive, and it requires more advanced technology and craftsmanship. There are some disadvantages as well, such as being necessary.
We will introduce the 5-axis processing machine on another occasion in the future.