007 Milling: Seemingly simple but difficult hole machining
1. What shapes are difficult to drill holes in?
There are surprisingly many problems related to hole machining during cutting.
Last time, we introduced curves in deep holes and swells caused by holes that are close to the wall.
This time, we will introduce an example of hole machining that seems possible at first glance, but is difficult to process.
I think that just by keeping these examples in mind, you will be able to greatly reduce problems from a manufacturing site perspective.
2. Back counterbore on flange surface
By drilling a counterbore hole, you can fill in the head of the cap bolt for a cleaner look.
However, it is not necessarily possible to make a counterbore hole just about anywhere.
A counterbore hole that is drilled from the opposite side to the tool approach direction is called a back counterbore.
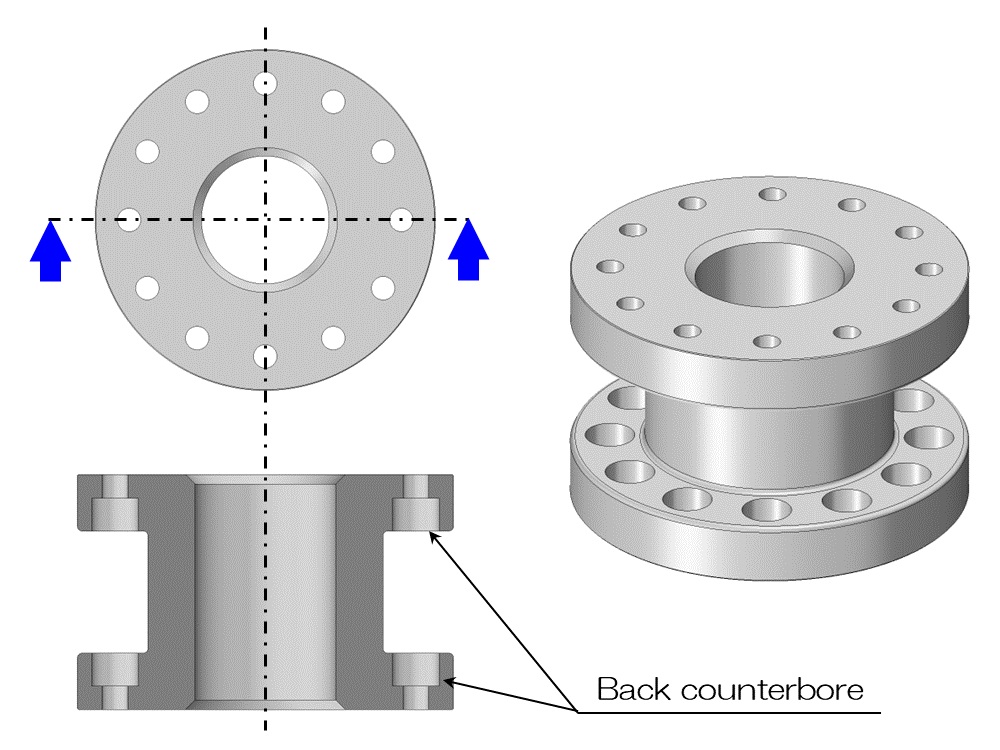
For example, let's imagine a back counterbore drilled into the flange surface of a piping component as shown in the diagram above.
Is this kind of shape possible?
Basically, this is difficult to achieve.
The reason is that when you try to counterbore, the flange in the front gets in the way.
This type of shape that is a shield in front of the shape you are trying to approach is also called an undercut.
Basically, it is difficult to process undercut parts during cutting.
It may be possible to achieve this by forming a counterbore shape using die-sinking electric discharge, using an angle head that rotates the spindle at a 90° angle, or using a special tool for back counterboring.
Alternatively, it may be possible to achieve this by dividing the parts and welding them together.
In either case, special tools and separate processes are required, resulting in an irregular shape.
It is probably best to avoid back counterboring unless it is absolutely necessary.
3. A hole too deep to open
For example, it is often difficult to process holes that are too deep from the opening, such as holes drilled in the bottom of a cylinder.
You need to be especially careful when approaching from the other side, such as in a blind hole.
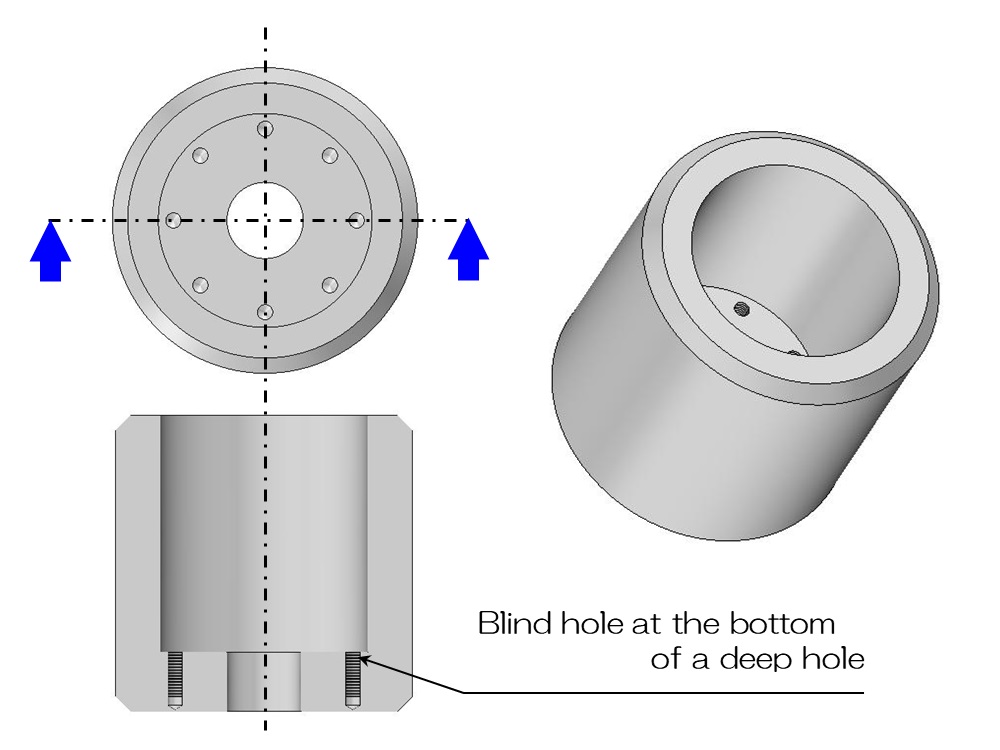
As shown in the diagram above, if the surface where the hole is drilled is deep and the hole is blind and can only be approached from the opening, the required overhang is often too long and machining is difficult.
This is especially true if screw holes or tolerance holes are specified.
If you can open it from the other side and penetrate it, this is an easy solution.
Alternatively, you could consider making the bottom part separately and joining it by welding or bolting.
Deep blind holes tend to have irregular shapes, so be careful when designing them.
4. Undercut hole
Please note that it may be difficult to create a blind hole in the flange depending on the direction.
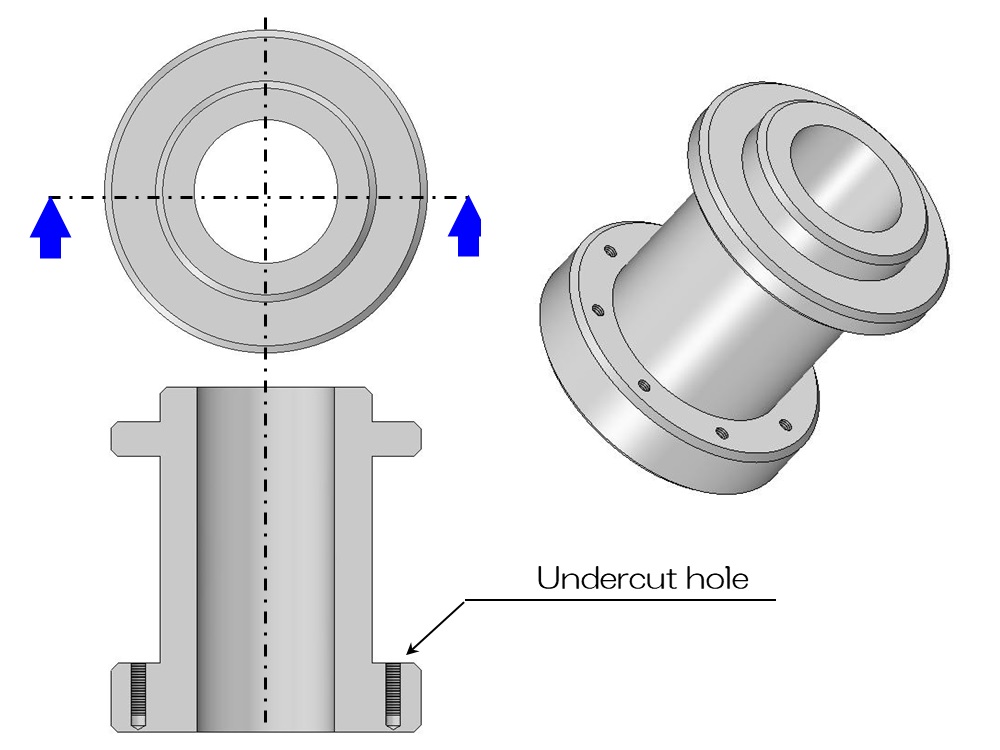
A typical example is the one shown above.
The situation is similar to the back counterbore described above, and the flange on the front gets in the way when drilling holes.
When this happens, it is difficult to process with general cutting machines.
Although it looks simple, it is actually a difficult part to machine.
If the penetration is OK, the difficulty of machining will drop immediately.
First, consider whether it is okay to go through it, and whether an undercut hole is really necessary, considering the purpose of the design.
Hole drilling is a process that is particularly prone to problems.
Although it may seem simple at first glance, there are cases in which it becomes a big fuss at the actual manufacturing site.
Avoid unreasonable designs by imagining the manufacturing process in advance.
The shortest way may be to feel free to consult with the manufacturing site.