015 Milling: Avoiding detortion by design
1. Detortion of thin parts
As explained previously, due to the nature of milling, which removes volume, deformation is particularly likely to occur in thin objects.
Since physical deformation occurs, there is a limit to the accuracy that can be achieved in removing warpage and straightening at the manufacturing site.
I would like you to consider changing the shape to a shape that is less likely to cause deformation on the design side.
This time, we will introduce an example of a design change for a thin component that is prone to deformation.
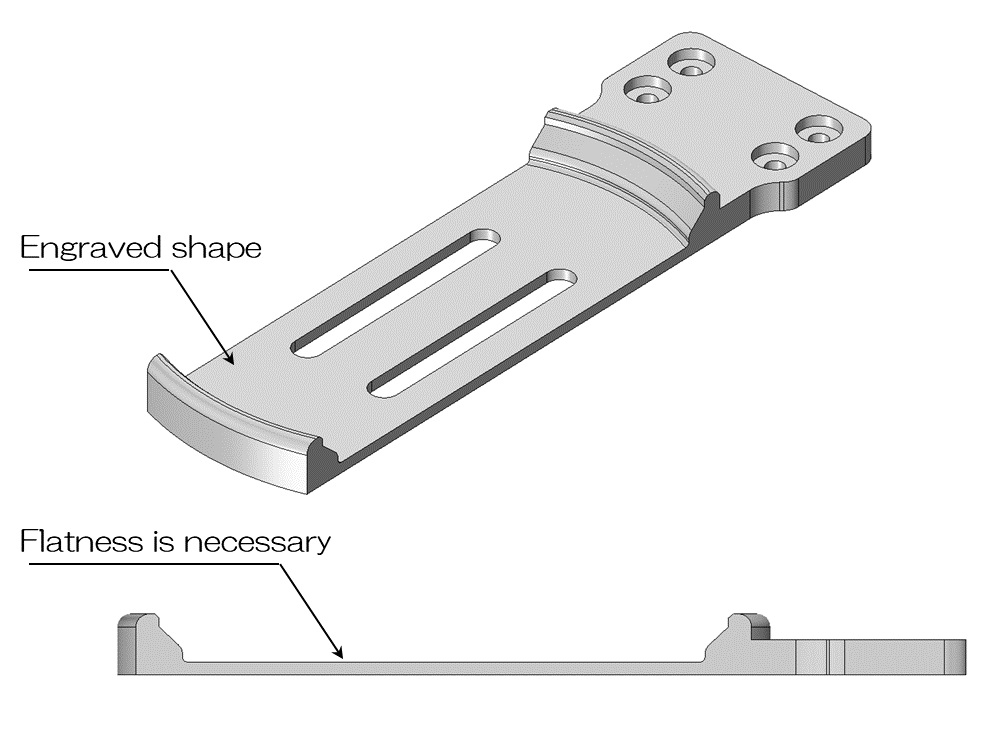
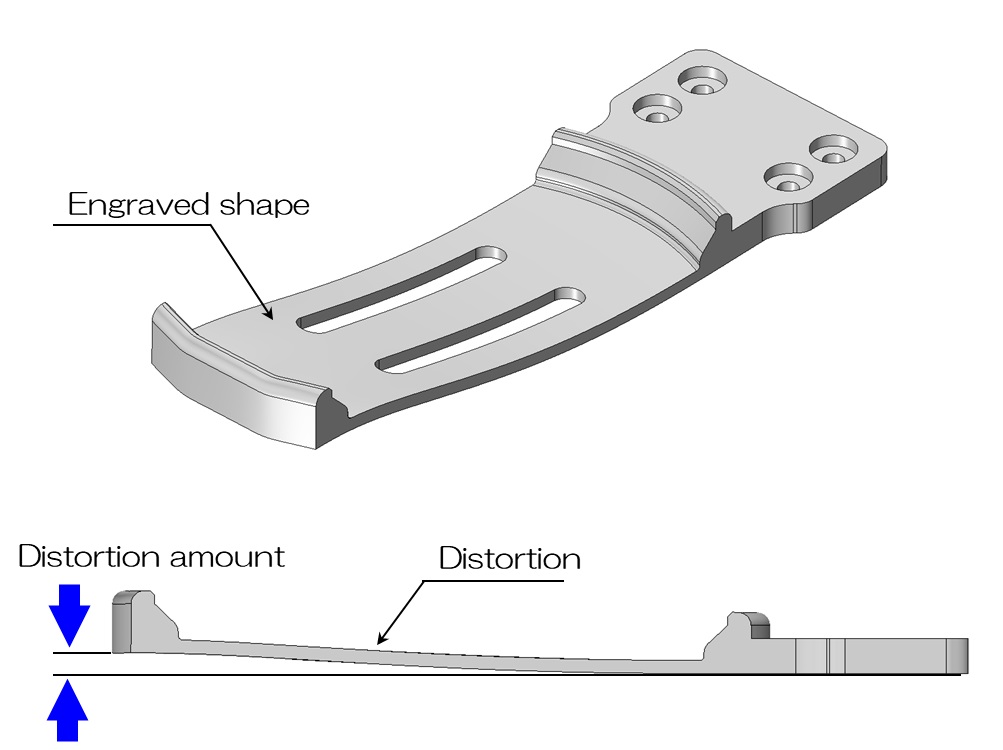
The above figure is an example of arm parts used for transportation by robots, etc.
Ideally, it would have a flat finish as shown on the left, but in reality, stress causes deformation as shown on the right.
To prevent this deformation as much as possible, the following are the main measures that can be taken on the design side.
- Reduce the amount of milling by keeping the height as low as possible
- Make the bottom as thick as possible
- Add reinforcement to the back
2. Reduce the amount of milling
The greater the amount of removal, the greater the deformation.
In an example like this, if there is room for improvement, such as lowering the wall height of the dug-out part, it should be possible to reduce the deformation by lowering it as much as possible.
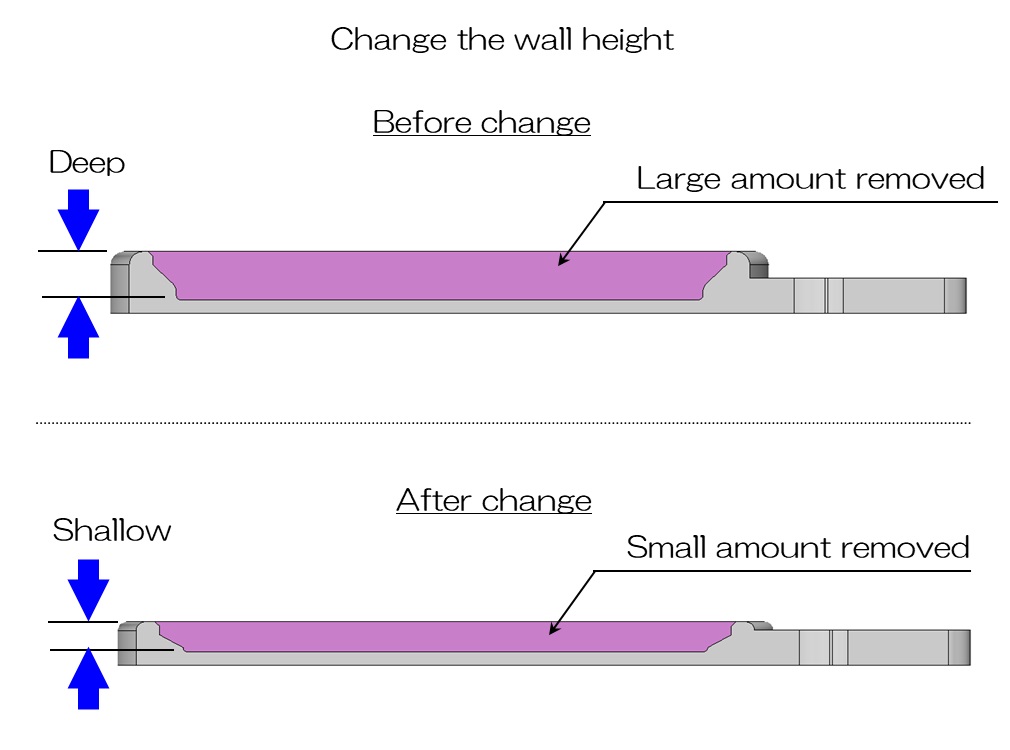
If you lower the wall height as shown in the diagram above, the amount removed by milling (pink part) will be reduced as a result.
This will also reduce the amount of deformation.
It is a good idea to reduce this depth of excavation to the extent that the design allows.
3. Make the bottom as thick as possible
If you cannot change the height of the wall, the next option is to make the bottom thicker.
Even if the amount removed is the same, the amount of deformation will be smaller as the thickness of the part that remains is greater.
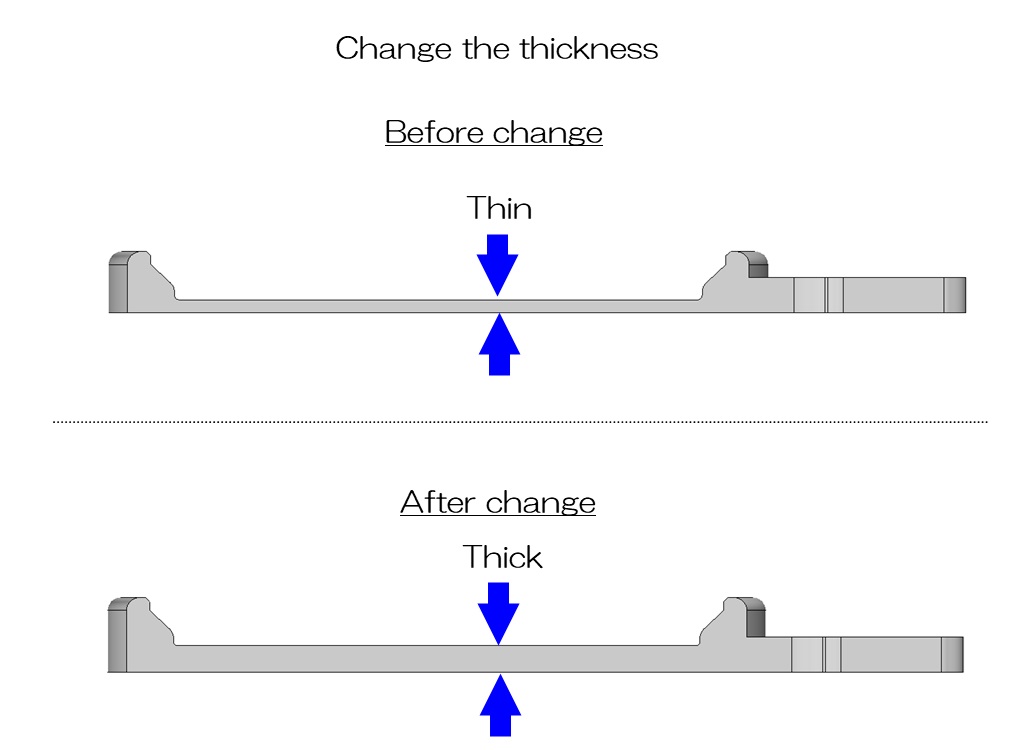
As shown in the diagram above, making the wall thickness as thick as possible will minimize deformation.
However, the material will be larger and the weight of the parts will also increase.
I think it would be a good idea to consider this as one direction when considering trade-offs.
4. Add reinforcement to the back
If there are restrictions on the shape or plate thickness of the dug-in part and changes cannot be made, please consider adding a reinforcing shape if it is permissible.
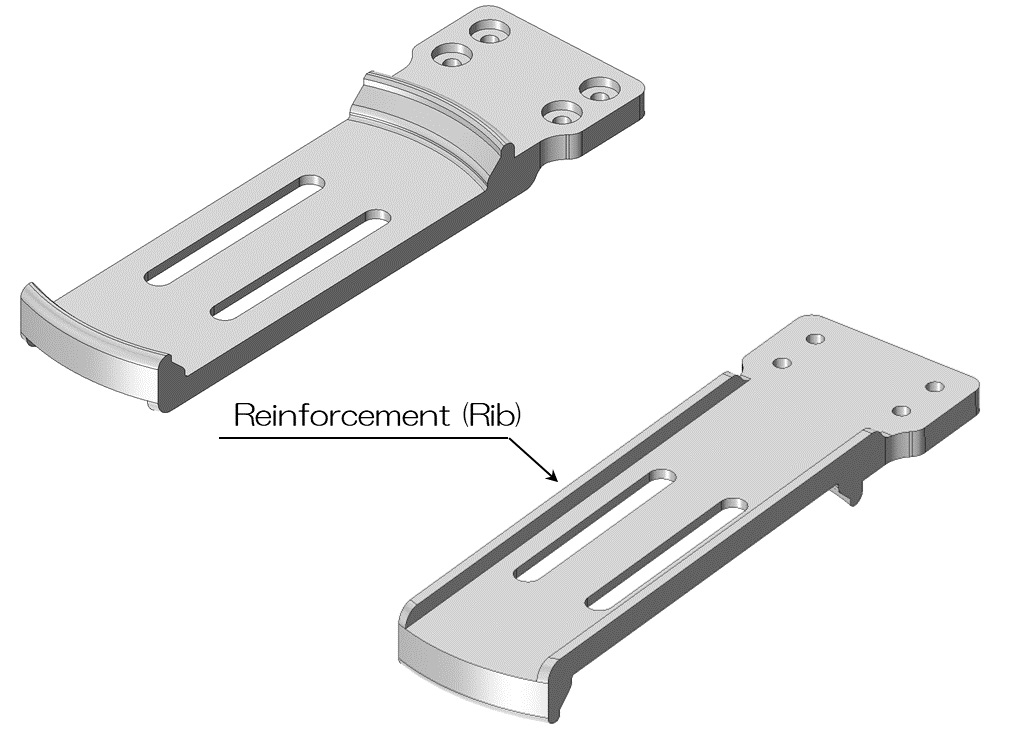
For example, in a shape like this one, adding longitudinal reinforcement to the back side may greatly suppress deformation.
Of course, careless addition of shapes may cause unexpected deformation, so you need to be careful.
Of course, the material will be larger, and the processing time and weight will also increase, so you need to carefully consider the advantages and disadvantages before making a decision.
When designing thin parts, we would appreciate it if you would consider incorporating measures to prevent deformation as much as possible on the design side.