014 Milling: Destortion of thin shape
1. Destortion of thin parts
Milling process can be said to be an essential process for manufacturing precision parts.
This is an indispensable processing method for machines and equipment that require precise movements.
Cutting, as it is called removal processing, is a process that removes unnecessary parts from a material.
In fact, this feature is also a method that can cause major problems.
Stresses remain balanced inside the material.
By forcibly removing the material, the residual stress that originally existed in the material is released, and processing stress is added due to processing, which disrupts this balance.
Particularly thin parts or parts that require a large amount of material to be removed will be deformed after processing due to the effect of this stress.
For example, consider the following parts.
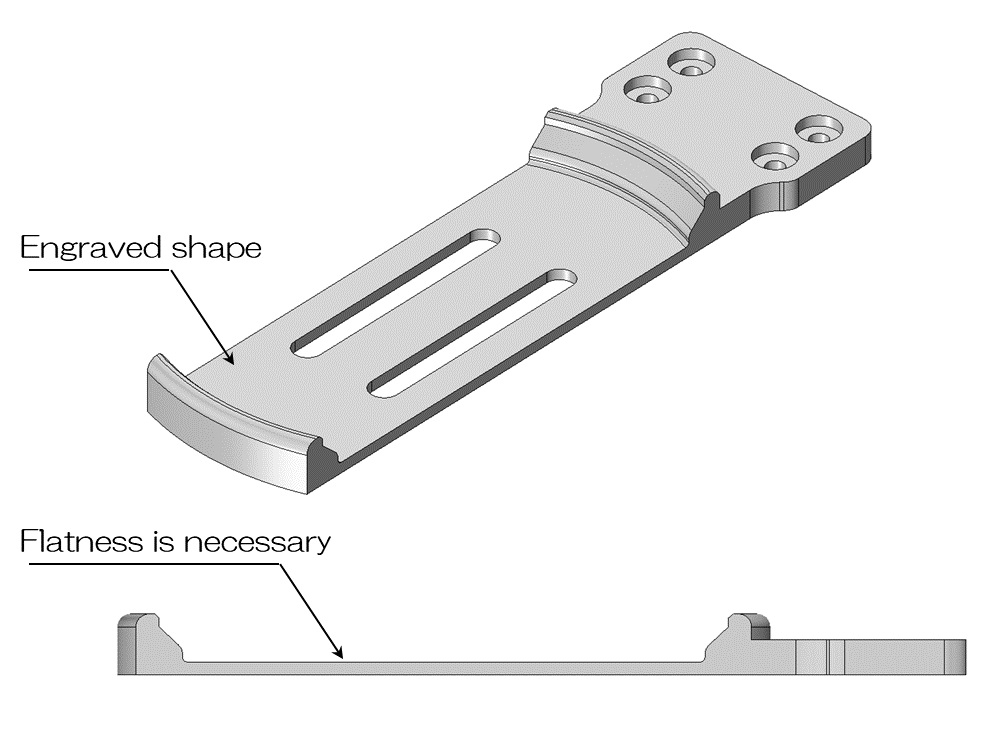
The arm shown in the diagram above is a part that is used in the arms of transportation robots.
It functions to rescue and transport cylindrical and disc-shaped parts.
Such parts have recesses to assist the other part, but it is important that the bottom surface is flat.
In such cases, it is extremely difficult to manufacture the product as designed.
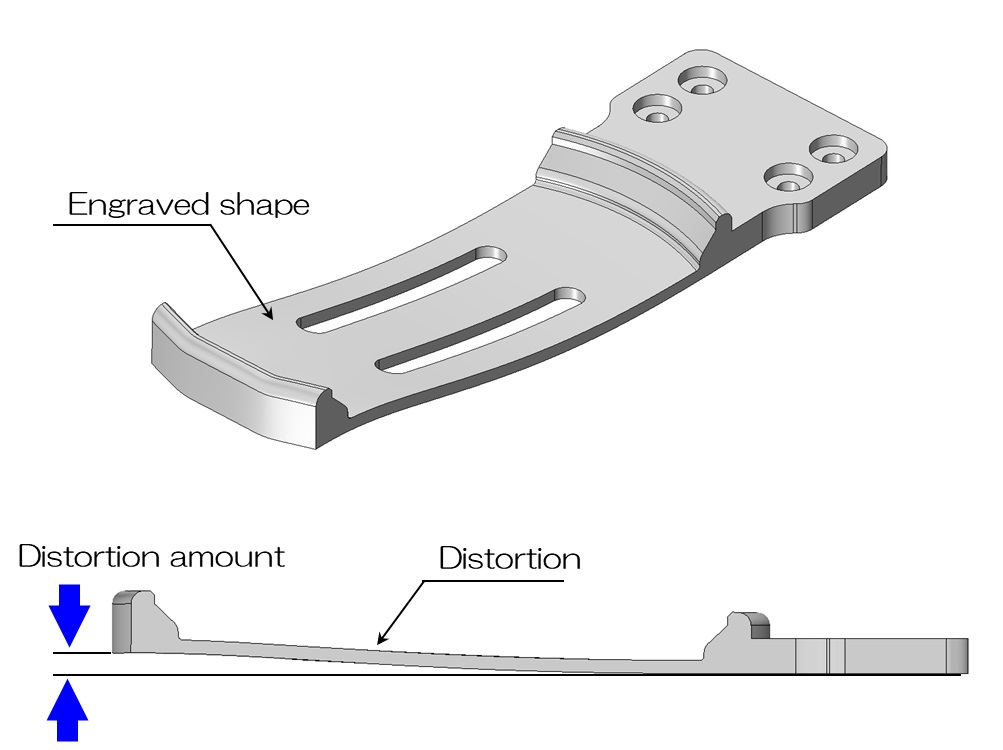
If you process something without thinking about it, deformation will occur as shown in the diagram above.
Although the above situation is a considerable exaggeration, this kind of deformation occurs to a greater or lesser extent.
It is common for a deformity to occur, as if the area where the removed part is larger is bowed.
2. Distortion of plate parts
Let's take a look at another thin parts.
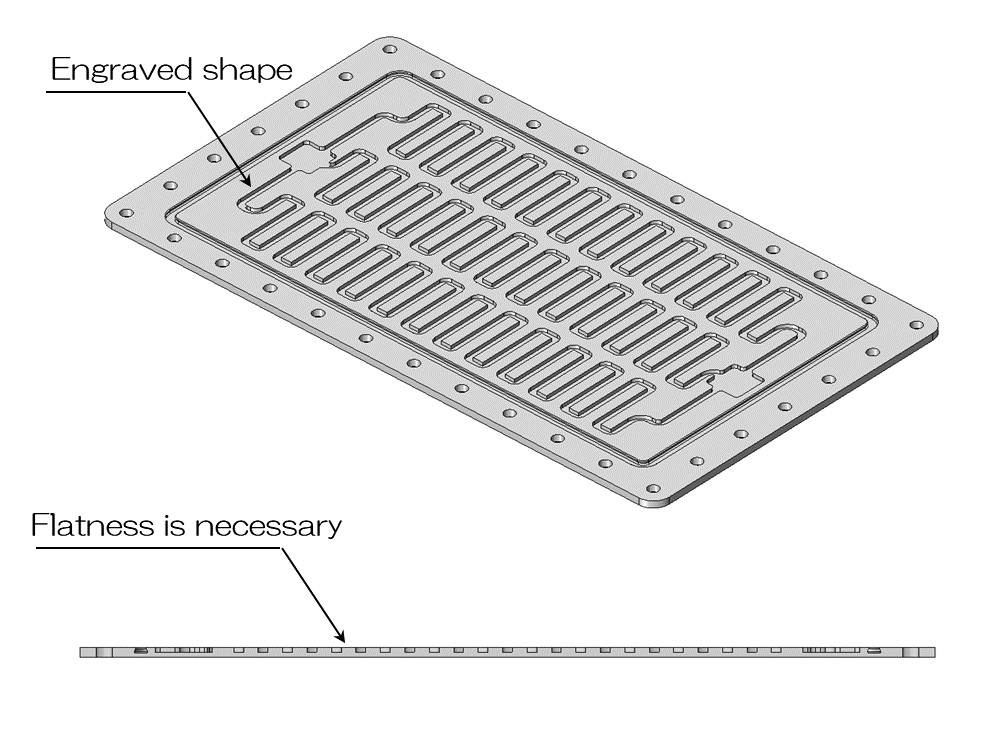
A typical example is a plate part with a flow path carved into it, as shown in the diagram above.
Especially if you dig only from one side, there will definitely be warpage.
Ideally, it would be finished flat as shown in the image above, but realistically it would look like the image below.
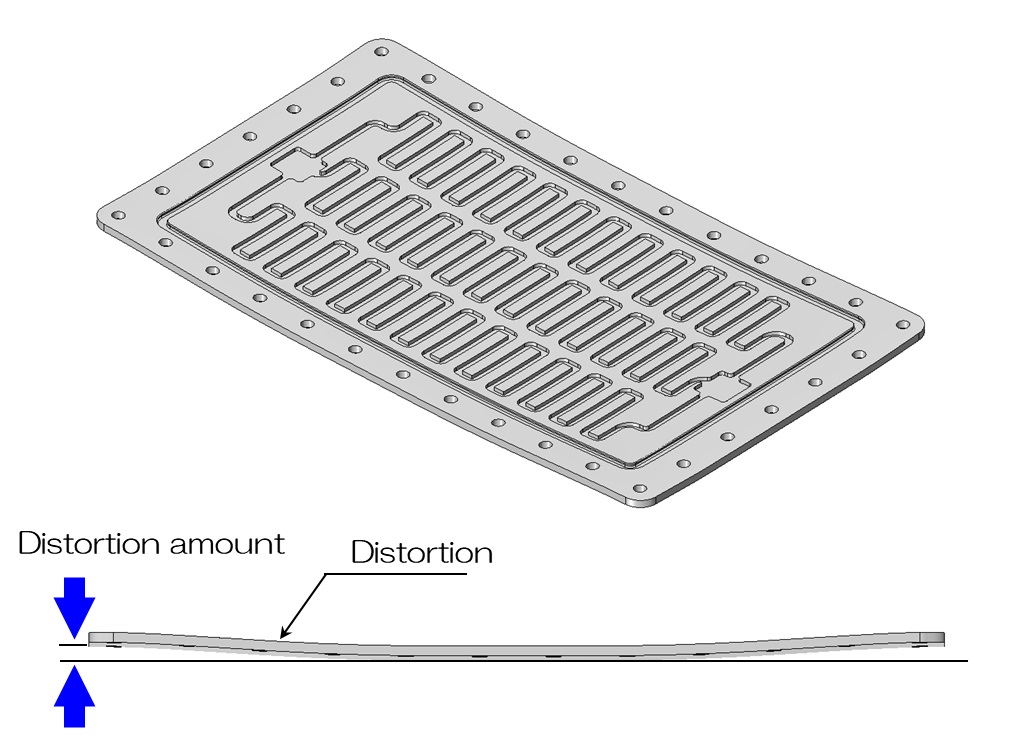
In this way, if you place it without applying any force, it should be deformed so that both sides warp.
3. How to reduce warpage through processing
When processing such thin products, it is possible to minimize deformation as much as possible through ingenuity at the manufacturing site.
The main methods are:
Annealing (annealing treatment) removes residual stress
This is a method to remove residual stress by heat treatment before machining or during rough machining.
Deformation can be suppressed to some extent by finishing after residual stress is removed.
Repeat the warping process
During the rough machining stage, the clamp is released once and the top and bottom surfaces are shaved to reveal the deformation (warpage removal machining).
After that, further processing is performed, and the clamp is released again to reveal the deformation and remove the warp.
While performing this warping process, rough machining is carried out, and after the deformation is suppressed as much as possible, finishing machining is performed.
Improvement of processing conditions and tools
We will explore conditions to minimize deformation by optimizing machining conditions (spindle rotation speed, feed rate, depth of cut, etc.), changing the shape and material of the end mill, and devising the type and application of cutting oil.
Correction after processing
Basically, deformation becomes obvious after the clamp (fixation) is released.
In most cases, there is no deformation when it is clamped to a processing machine.
In other words, as long as you correct it, you should be able to produce highly accurate machining.
In such cases, there are cases where the deformation is corrected using a press, etc. after processing is complete.
Deformation can be suppressed to some extent by the measures mentioned above at the manufacturing site.
However, due to the principle of removal processing, deformation will inevitably occur.
In many cases, it would be more reasonable to assume that these shapes will deform, and then devise ways to avoid this in the design.
Next time, I will introduce how to improve the design.