005 Milling: Basics of hole machining
1. Basic flow of hole drilling
Hole drilling is a very important element in machining.
This time, we will introduce the basic flow of hole machining.
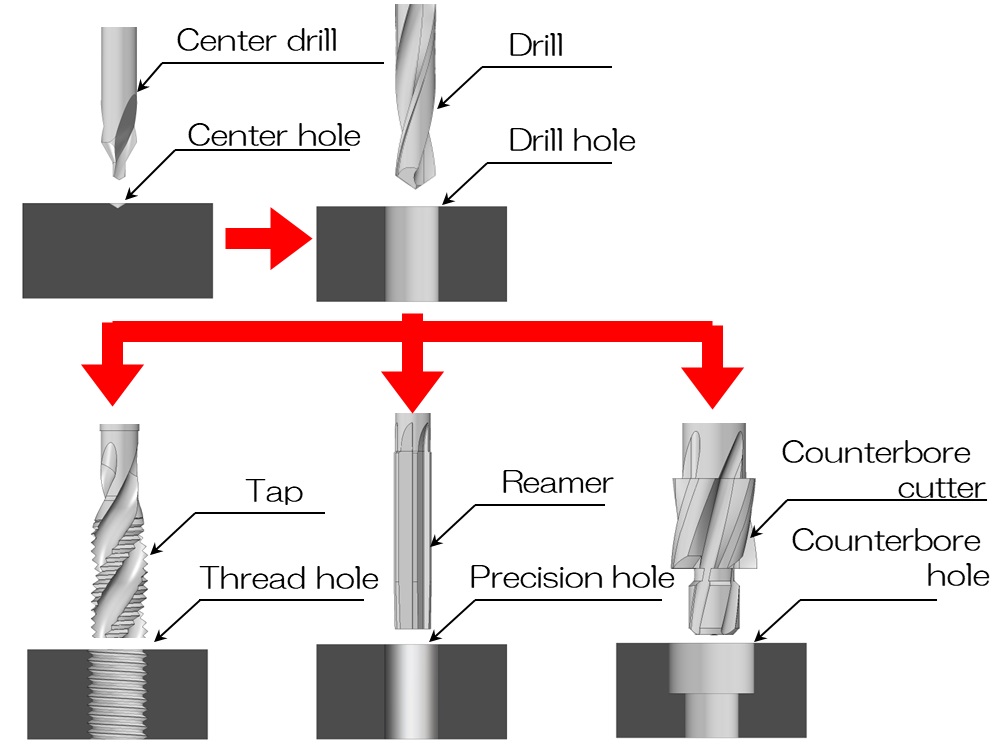
When machining holes, positional accuracy is often required, so first drill the center hole with a center drill.
This center hole acts as a so-called punch and serves as a guide during drilling.
Next, perform drilling.
When drilling large holes, the drill may be gradually expanded from a small diameter drill to a larger drill.
The hole made with this drill is what is called a drilled hole.
Holes for screws require a certain amount of play, so this is often the case.
If a thread hole is required, then use a tap to machine the thread hole.
For NC machining, we use a code called tap cycle, which is dedicated to machining thread holes.
If a tolerance hole with high dimensional accuracy is required, reaming is performed.
This makes it possible to machine holes with a smooth inner surface and high precision tolerances.
Reaming may also be performed using a dedicated code called a boring cycle.
To counterbore the head of the cap bolt, use a counterbore cutter to create a stepped hole.
In this way, the basics of hole machining is to change the shape of each hole to the required shape based on the drill hole.
2. Features of incomplete shapes
The most important thing to be careful about when tapping or reaming is that each tool has a part that is not perfect in shape, so it is necessary to create a pilot hole that is longer than the effective length in order to release that length. It is necessary.
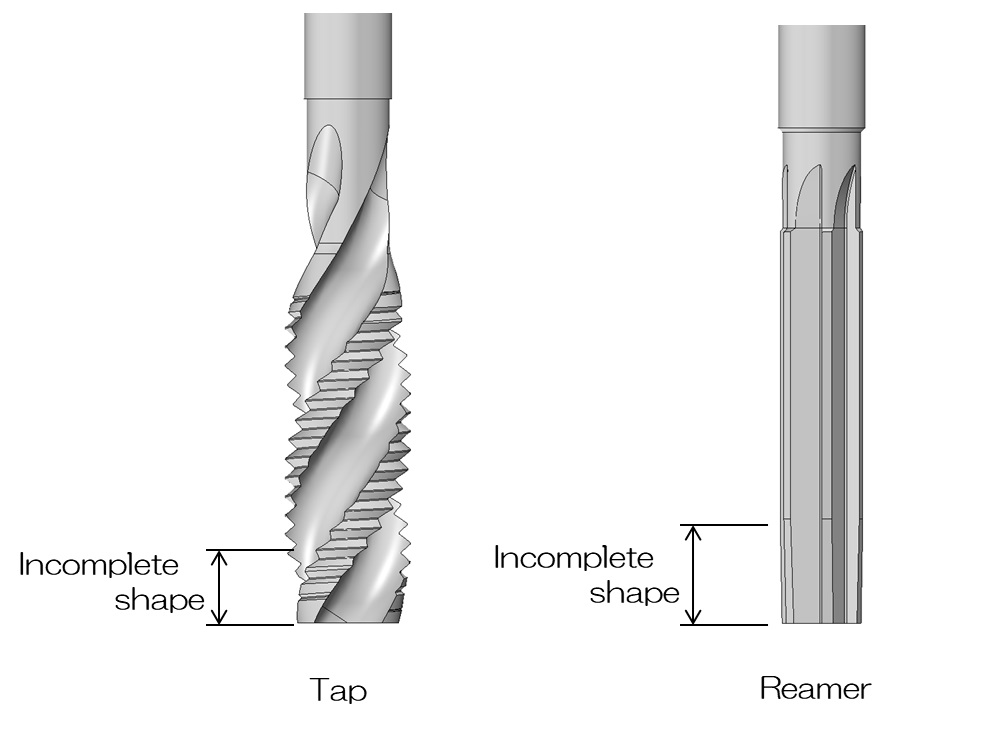
As shown in the diagram above, the tips of taps and reamers are tapered to smoothly enter holes and reduce cutting resistance.
Naturally, this part will transfer an incomplete shape.
If you design without being aware of the existence of these imperfections, unexpected problems may occur.
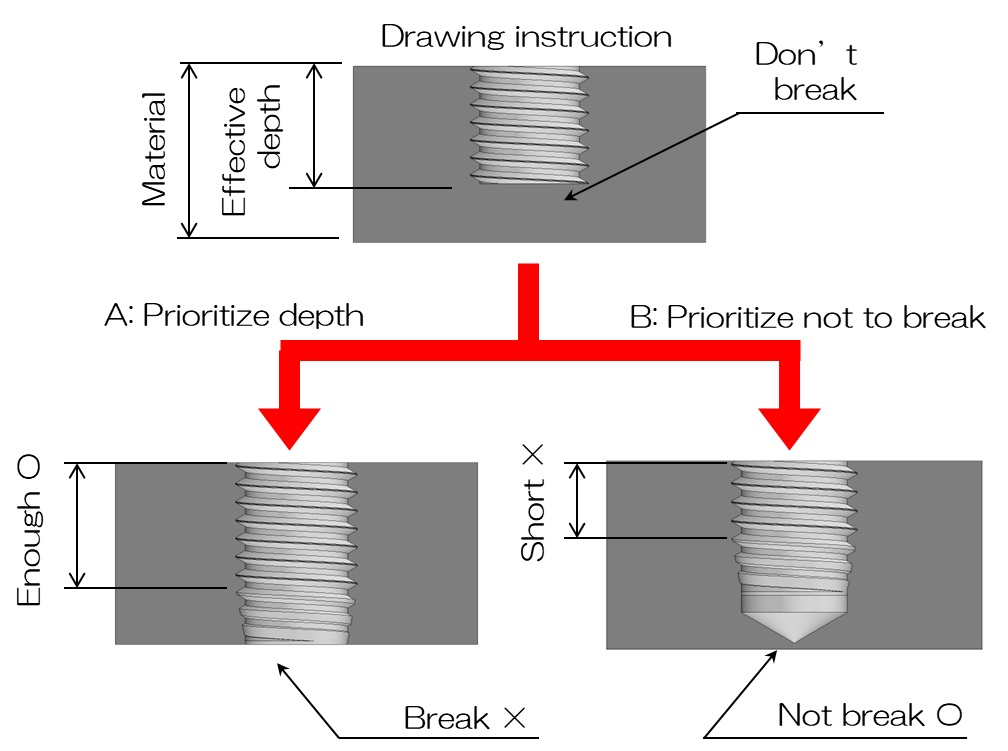
As shown in the diagram above, if you specify a screw hole where the effective length of the screw is at the limit for the thickness of the material, and tearing to the back side is not acceptable, you may receive complaints from the manufacturing site.
Let's assume that the instructions in the drawing are as shown above.
Although the design appears to be complete at first glance, it seems that the existence of imperfections and pilot holes have been forgotten.
If you actually prioritize securing the effective length of the screw, the pilot hole will end up penetrating the back side as shown in A, resulting in tearing.
On the other hand, even if the pilot hole is drilled just enough to prevent tearing as shown in B, the effective length of the screw cannot be secured this time.
In any case, it cannot be processed according to the drawing.
There is also a type of thread cutting tool called a planet cutter that requires almost no extension of the pilot hole.
However, the program for thread cutting with a planet cutter is special and the tool cost is high, so I think it is better not to choose it unless you have a serious need.
I think you can avoid problems by always keeping in mind that there are imperfections in taps and reamers when designing them.
When drilling large holes that cannot be drilled with a drill, boring is performed if precision is required, or an end mill is used if accuracy is not required.