Various surface treatments
We also accept various surface treatments such as painting, plating, and polishing, as well as processing of materials such as resins, ceramics, and precious metals.
These materials are mainly used to prevent surface oxidation, such as iron and aluminum, and to add color and texture.
Plating
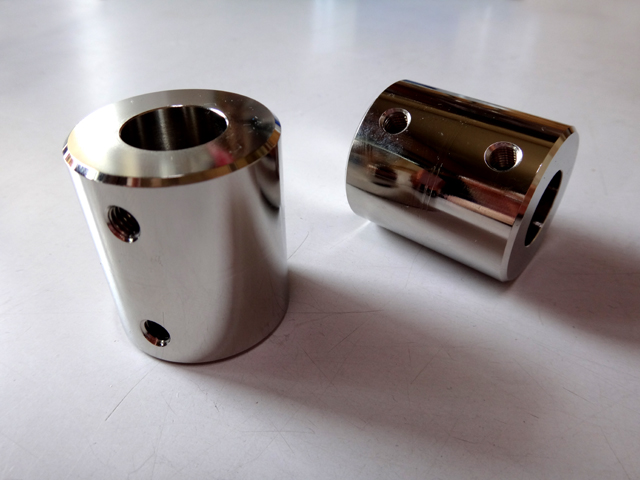
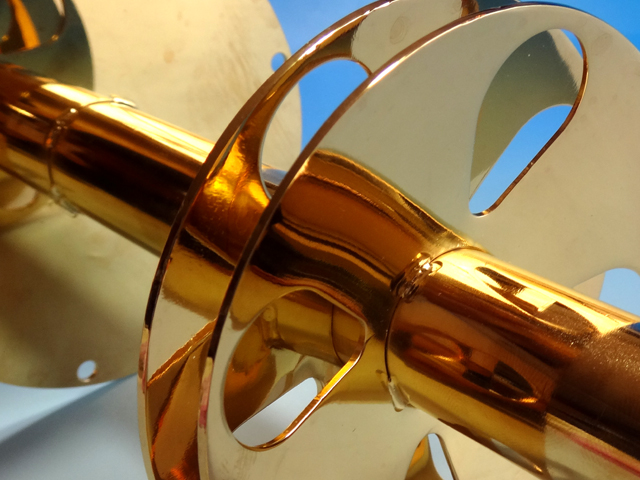
Various platings can be selected depending on the material and purpose, such as zinc plating (chromate, Unichrome, etc.), nickel plating (electrolytic nickel, electroless nickel, etc.), chrome plating (hard chrome, decorative chrome, etc.), and gold plating.
It is relatively easy to control the film thickness, and is used for a variety of parts as a means of surface treatment in large quantities and at low cost.
Type | Detail | Thickness | Hardness | Cost | Note |
---|---|---|---|---|---|
Zinc | Electro galvanized | around 10 micron meters | 60-90 HV | Reasonable | Glossy chromate (UNIQLO) Colored chromate Black chromate Trivalent chromate etc. |
Nickel | Electric nickel plating (bright) | 5-10 micron meters | 400-500HV | Standard | |
Electric nickel plating (semi-gloss) | 5-10 micron meters | 300-350HV | Standard | ||
Electroless nickel plating | 5-10 micron meters Controlable | 450-600HV | A little expensive | After quenching 800~1000HV | |
Chrome | Decorative chrome plating | 5-10 micron meters Chrome thickness: under 1 micron meter | around 700HV | A little expensive | Nickel coating after polishing |
Hard chrome plating | 10-30 micron meters | 800-1000HV | Expensive | Buff polishing before and after plating | |
Gold | Decorative gold plating | A few micron meters Gold thickness: 0.1 micron meter | - | A little expensive | Flash plating |
Industrial gold plating | - | - | - | Variable condition as required | |
*Numbers are general ranges (reference values)
Anodize
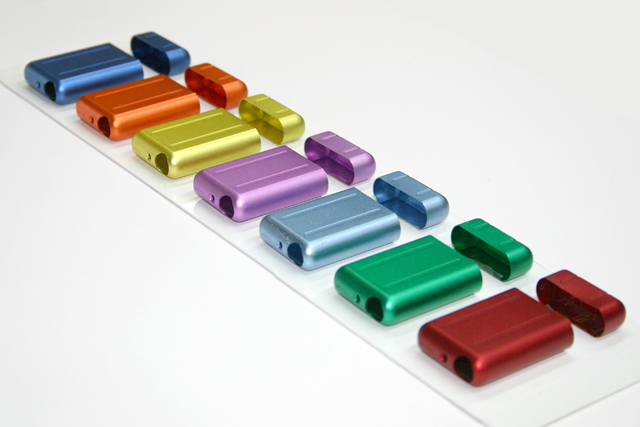
This is a surface treatment unique to aluminum. By immersing aluminum fabric parts in an acidic layer while applying electricity, the surface is replaced with aluminum oxide. Aluminum oxide has excellent corrosion resistance and wear resistance, and unlike plating, it is integrated with the base material, so there is no need to worry about it peeling off.
Generally speaking, for a membrane thickness of about 10 μm, the portion that erodes into the base material is approximately half, and the portion that protrudes outside the base material is approximately half.
Including regular white alumite and the frequently used black alumite, colored alumite using various dyes and pigments, hard alumite with a thick film of 20 μm or more, and metal ions encapsulated in the alumite layer to impart various properties. We can also handle derivative treatments such as secondary electrolysis.
Additionally, Taflam Treatment®, which is a combination of alumite and fluorine processing, improves corrosion resistance, wear resistance, and lubricity, and can be considered a type of alumite.
Polishing
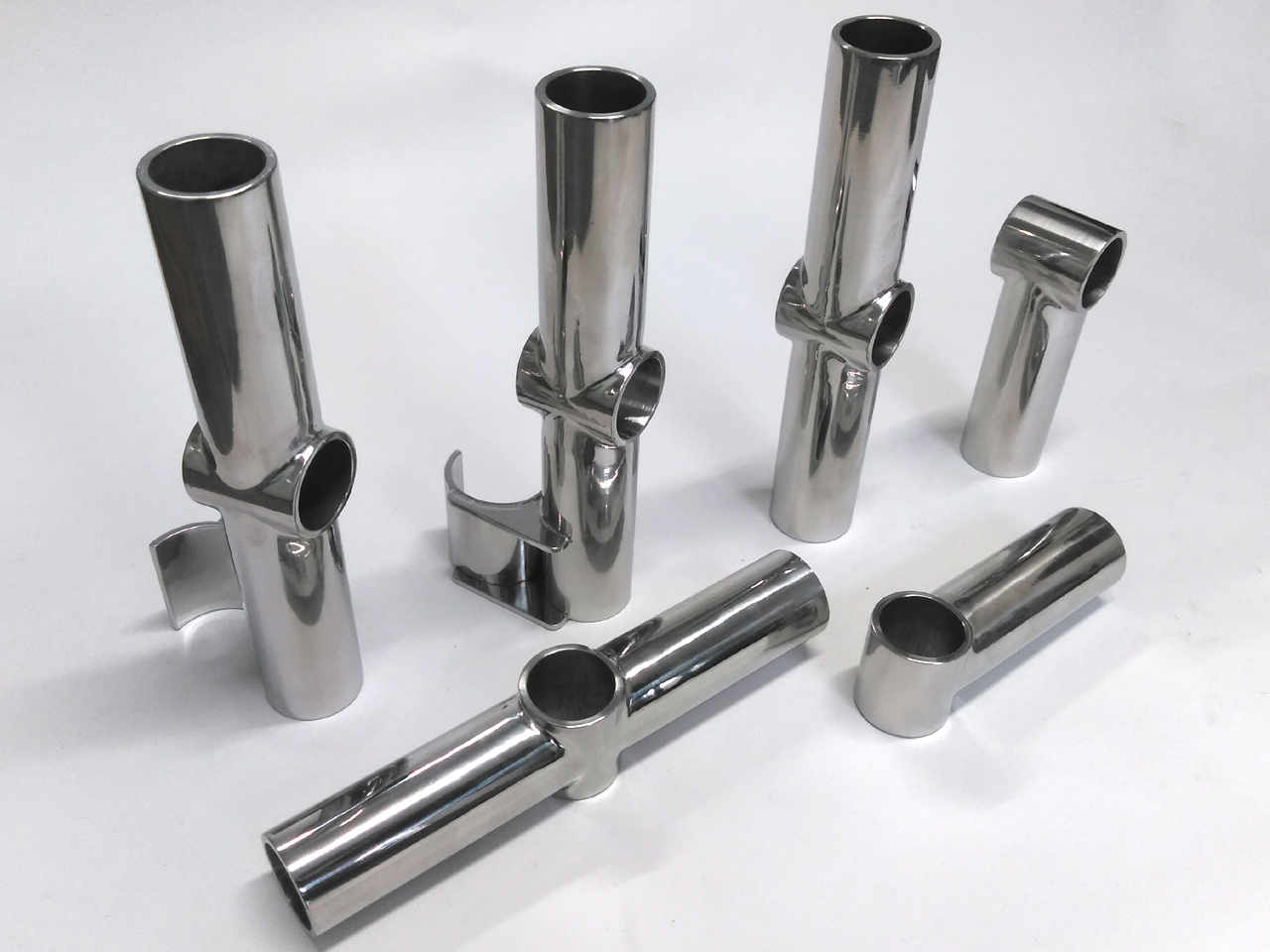
Polishing processes include buffing, fluid polishing, and electrolytic polishing.
Finishes the surface smooth and improves gloss.
In addition to improving appearance, it is often used in food, medical, and semiconductor-related parts to prevent the adhesion of impurities.
400 finish, mirror finish, and hairline finish are common for buffing.
We recommend "precision polishing" for polishing precision parts.
Precision polishing is a polishing process for precision parts that polishes parts to around Ra0.8 with almost no change in size or shape.
Blasting
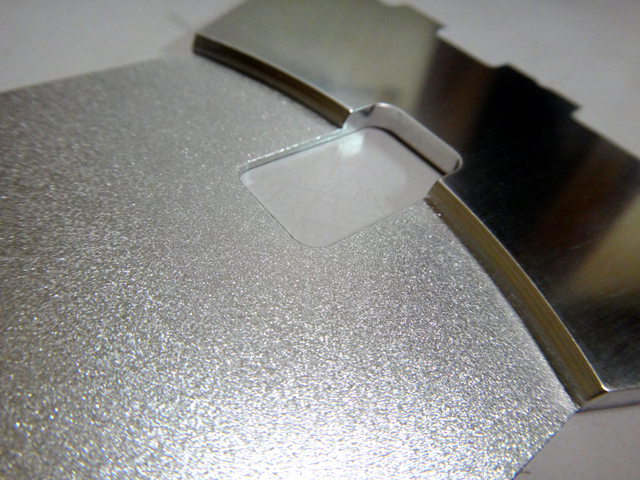
This is a processing method that sprays media such as alumina or glass beads to give the surface of the part a satin-like finish.
It is often used for surface treatment such as alumite, plating, and painting.
It is also used for purposes such as deburring parts and removing paint.
Please specify the type of media and particle size.
Painting
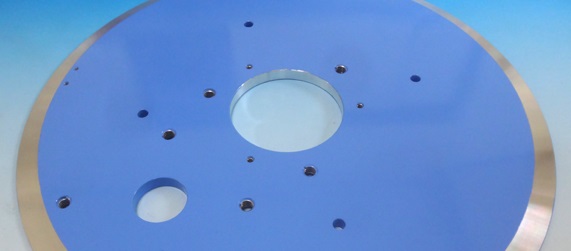
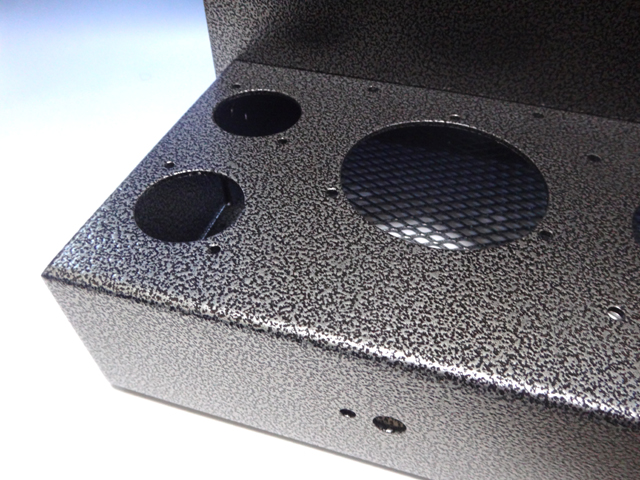
Mainly available for baking painting.
Baking coating is possible not only on iron but also on aluminum and stainless steel.
Important areas can be masked or painted separately.
You can specify a variety of options, including special coatings such as Leatherton and Hammerton, coatings with strictly specified colors, and urethane coatings for parts that cannot be heated.
We also accept coating processing that applies painting technology, such as fluorine coating.
Melamine baked paint
This is a general baked coating that uses melamine resin as the paint, hardens at low temperatures, and is easy to handle.
It is widely used because it can be applied to various metals. The heating temperature is lower (about 150℃) than that of acrylic resin baking paint.
<Advanteges>
It is easy to apply thickly and is highly decorative.
Cheaper than acrylic baked paint.
<Disadvantages>
It is easily deteriorated by ultraviolet rays and is not suitable for use outdoors for a period of time, as the color may fade due to aging.
Acrylic baking paint
It is a baked coating using acrylic resin as the paint. Although it tends to be slightly more expensive than melamine resin baked paint, it has many advantages. Usually, Meamin paint is overheated at a high temperature of around 180℃.
<Advantages>
Hard surface and scratch resistant
High adhesion and difficult to peel off
Can also be painted on aluminum materials
Suitable for outdoor use as there is little deterioration due to UV rays.
<Disadvantages>
More expensive than melamine baked paint
Other painting
In addition to the general melamine baked paint and acrylic baked paint, we also support various types of coatings.
Fluorine baking paint:
It has better weather resistance than acrylic baked paint, and also has excellent water and chemical resistance. Although it can be said to be an excellent coating that can withstand long-term use, it also comes at a high cost.
Epoxy baking paint:
It is characterized by its high adhesion, which makes it difficult to peel off, and its dimensional change when heated and cured is small. It is used for painting large structures for rust prevention purposes. Because it deteriorates in sunlight, it is mainly used as a base coating.
Silicone baking paint:
It is characterized by high heat resistance. Used for cooking utensils, etc.
Urethane paint:
Unlike baking coating, this coating method cures by air drying at room temperature, so it is used for coating materials such as resin that cannot be heated, and large parts that cannot be coated with baking coating.
It provides a finish comparable to baked paint and has weather resistance, but because it takes a long time to harden, there is a risk of dust etc. adhering to it.
Hammerton painting/Leatherton painting:
Highly decorative coatings that have unevenness on the painted surface, such as hammerton coating, which creates a pattern that looks like the surface has been struck with a hammer, and leatherton coating, which has a leather-like surface.
Various heat treatments
In addition to surface treatment, we also handle various heat treatments.
Heat treatment includes overall heat treatment such as hardening/tempering and annealing, and surface hardening such as induction hardening and nitriding.
Please make a request at your convenience.
Whole heat treatment
Whole-body heat treatment involves heating and cooling the entire part to cause changes in the part's structure.
"Quenching/tempering", "annealing", and "normalizing" are common.
Quenching/tempering
Quenching is the process of heating steel containing carbon to change it to a structure called austenite, and then rapidly cooling it to change it to a hard structure called martensite.
Quenching is written as HQ in the JIS symbol.
Quenching makes it hard, but it also makes it brittle, making it unsuitable for use as a part. Therefore, it is heated again to a lower temperature than the temperature used during quenching, and then slowly cooled to improve its viscosity (toughness). The process to increase the quality is "tempering".
Tempering is written as HT in the JIS symbol.
The higher the reheating temperature during tempering, the lower the hardness and the higher the viscosity.
"High-temperature tempering" is a method of reheating at a high temperature to increase stickiness over hardness, and "low-temperature tempering" is a method of reheating at a low temperature to give priority to hardness over stickiness.
Usually, quenching and tempering are performed as a set (HQ/HT).
In addition, the heat treatment that involves high-temperature tempering after quenching to adjust hardness, strength, toughness, etc. is called "refining."
In particular, carbon steels such as S50C and SCM440 are often used as "tempered materials" that have been tempered to the extent that they can be machined.
It is also sold as "pre-hardened steel" (NAK55, DH2F, STAVAX, etc.) by various material manufacturers.
The hardness of tempered materials is often adjusted to a range of HRC30 to HRC40, which allows for cutting.
Annealing
Annealing is a heat treatment in which the material is heated and then gradually cooled to make the structure uniform and soft, remove internal stress, and improve machinability.
Annealing is written as HA in the JIS symbol.
In particular, it is often used to reduce distortion by annealing the condition of the material and after rough machining, such as thin machined products.
Normalized
Normalizing is a method of ensuring mechanical properties by uniformizing and refining the structure of materials manufactured under stress through casting, forging, or rolling through heat treatment.
In the JIS symbol, normalizing is written as NR.
Surface heat treatment
Induction hardening
Induction hardening is a method of heating only the surface to over 800℃ using induction heating using an AC power source, and is mainly used to improve the hardness and fatigue resistance of shaft-shaped and gear-shaped parts.
In the JIS symbol, induction hardening is expressed as HQI (Induction Hardening).
Utilizing the principle that the surface of a component is rapidly heated by resistance heat, only the vicinity of the surface is heated by placing an electric heating coil close to the component and passing a high-frequency induced current through the coil. The toughness is then restored by tempering at low temperatures.
<Features>
Induction hardening only hardens the surface, so the surface becomes hard and wear resistance improves, while the interior remains tough.
Since heat is applied only partially, deformation and dimensional changes are minimized.
The shape of the shaft may be bent or otherwise deformed after heat treatment, so the distortion is removed using a press, etc.
By hardening only the surface, compressive residual stress is generated on the surface, improving fatigue resistance.
・The surface hardness due to induction hardening is slightly harder than normal hardening/tempering.
・Induction hardening is said to be an environmentally friendly heat treatment because the heating time is short.
・Unlike whole-body hardening, another feature is that you can specify the parts to be hardened and the depth of hardening.
Nitriding
Nitriding is a method of increasing the hardness of the surface of parts using nitrogen compounds, and includes gas nitriding, salt bath nitriding, gas soft nitriding, and ion nitriding.
This is a process that hardens the material by exposing it to an atmosphere containing ammonia or nitrogen at a temperature below the austenitizing temperature, allowing nitrogen to penetrate near the surface.
In the JIS symbol, nitriding is written as HNT.
<Features>
・Since there is no need to raise the processing temperature, there is no need for post-processing heat treatment, and it is characterized by less deformation.
・Divided into nitriding treatment, which hardens to about 1000HV, and soft nitriding treatment, which hardens to about 600HB.
・Nitriding is mainly used to harden the surface and improve wear resistance.
・Nitrocarburizing treatment is mainly used to improve fatigue resistance.
Because the processing temperature is low, it is possible to improve the surface hardness of tempered steel while maintaining its internal hardness.
・It is known as a treatment that is also used for austenitic stainless steel such as SUS304 and SUS316.
・The thickness and hardness of the nitrided layer change depending on the processing temperature, and the thickness of the nitrided layer is approximately 0.1 to 0.5 mm.
It is divided into nitriding treatment, which hardens to about 1000 HV, and soft nitriding treatment, which hardens to about 600 HB.
Carburizing
Hardening steel requires carbon, so steels with a high carbon content such as carbon steel can be hardened, but steels with a low carbon content such as low carbon steel cannot be hardened.
In such cases, carburizing is a method to increase the carbon content on the surface and harden it.
In the JIS symbol, carburizing is written as HC.
The carburizing agent is heated together with the parts to diffuse and infiltrate carbon into the parts' surfaces.
Depending on the type of carburizing agent, there are solid carburizing (charcoal), liquid carburizing (cyanide salt), and gas carburizing (hydrocarbon gas).
Carburizing involves heating at high temperatures for long periods of time, which alters the structure of the center of the part. For this reason, quenching/tempering is performed after carburizing.
<Features>
・Low carbon steel, which is sticky, cheaper and easier to work with than high carbon steel, is usually inferior in hardness. Carburizing can only increase the hardness of the surface, so you can take advantage of the good parts of low carbon steel and strengthen the weak parts.
Low carbon steels such as S15C and materials with low carbon content such as SCM415 are mainly used.
There are two depth regulations for the hard layer (hardened layer) obtained by carburizing: total hardened layer depth and effective hardened layer depth.
The effective hardening layer depth is "the distance from the surface to the depth of 550 HV when quenched or tempered at a temperature not exceeding 200℃" (from JIS G 0559).
The total hardening layer depth is the distance to the hardness of the material itself.
Although it is possible to specify the effective depth, many heat treatment companies only support a certain range.
It seems that processing is often done at an effective depth of about 0.3 to 1.5 mm.
Other types of surface hardening include flame hardening (JIS symbol HQF), electron beam hardening, and laser hardening.
Please contact us for details.