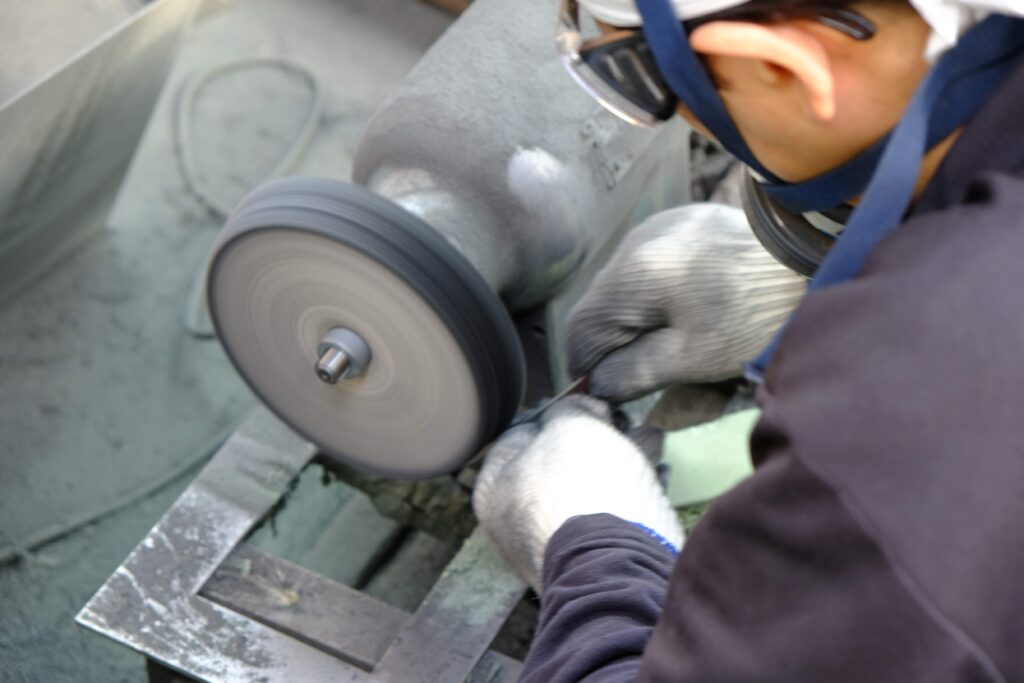
Ourt strength
The number of polishing companies in Tokyo is decreasing rapidly, but we have experienced craftsmen in-house and do everything in-house.
We use two polishing techniques, buffing and hand polishing, to meet the diverse polishing needs of our customers.
We specialize in polishing complex shapes that cannot be automated and are not suitable for mass production.
In particular, our advanced precision polishing technology that suppresses dimensional changes to around 1 to 2 μm is highly valued by customers who manufacture semiconductor manufacturing equipment, food, and medical machinery parts.
Features
One stop service
We handle everything from arranging parts (materials, sheet metal processed parts, machined parts) to secondary processing after welding. We can also undertake bead cutting and polishing for welding food machinery and medical parts.
2 polishing systems
By using two types of polishing technology: buffing and accurate polishing, we can meet a variety of polishing needs.
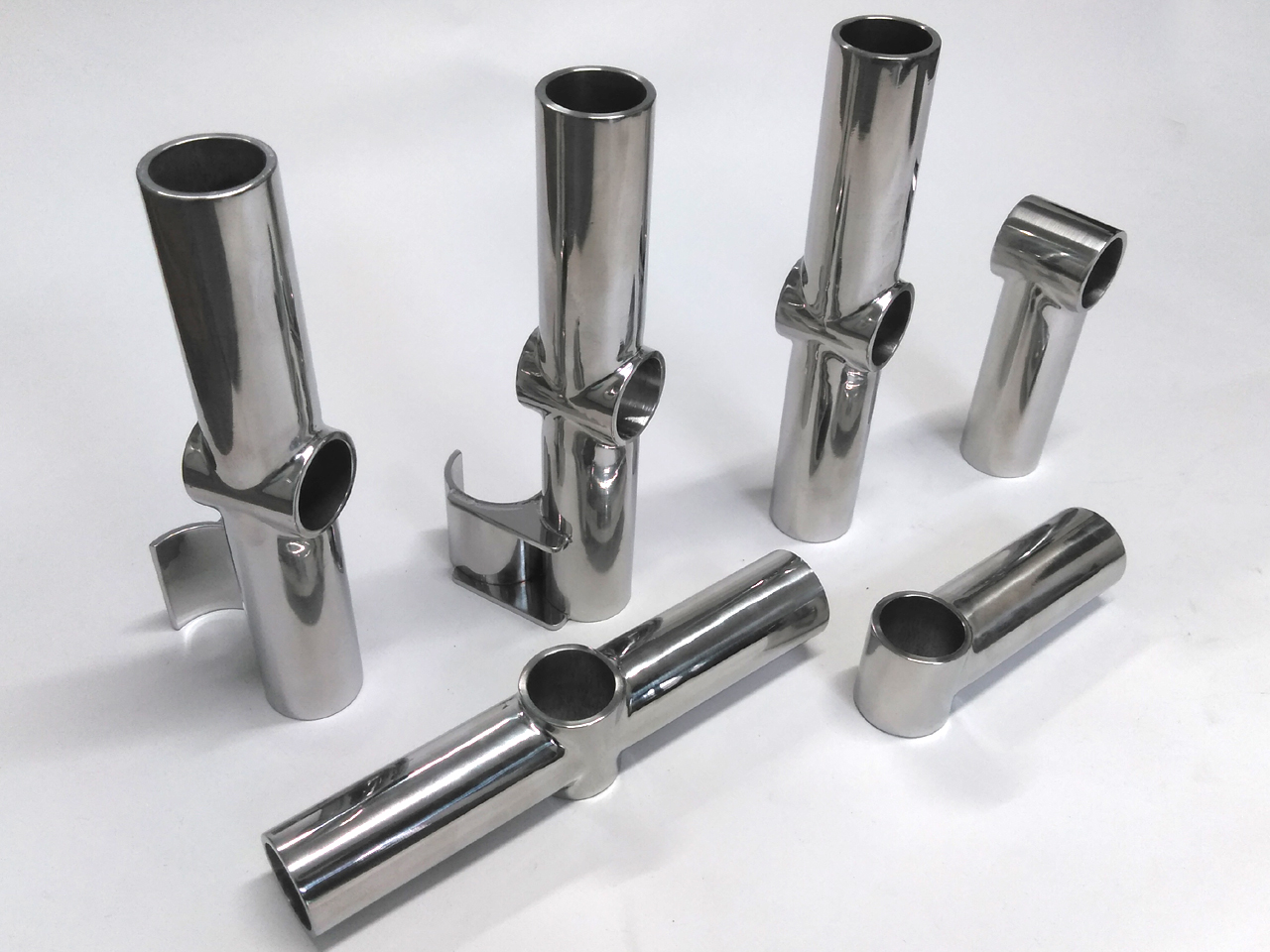
Skilled craftsmanship
Polishing is performed by skilled craftsmen with advanced technology that uses precision polishing to limit dimensional changes to around 1 to 2 μm.
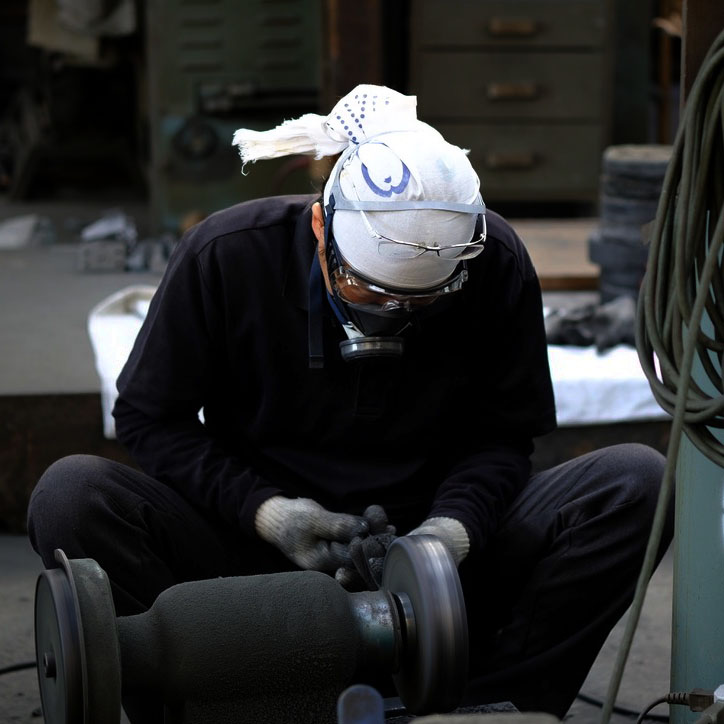
Rough polishing
Our experienced technicians perform rough polishing and semi-finish polishing, which there are currently very few polishing companies in Tokyo that can handle.
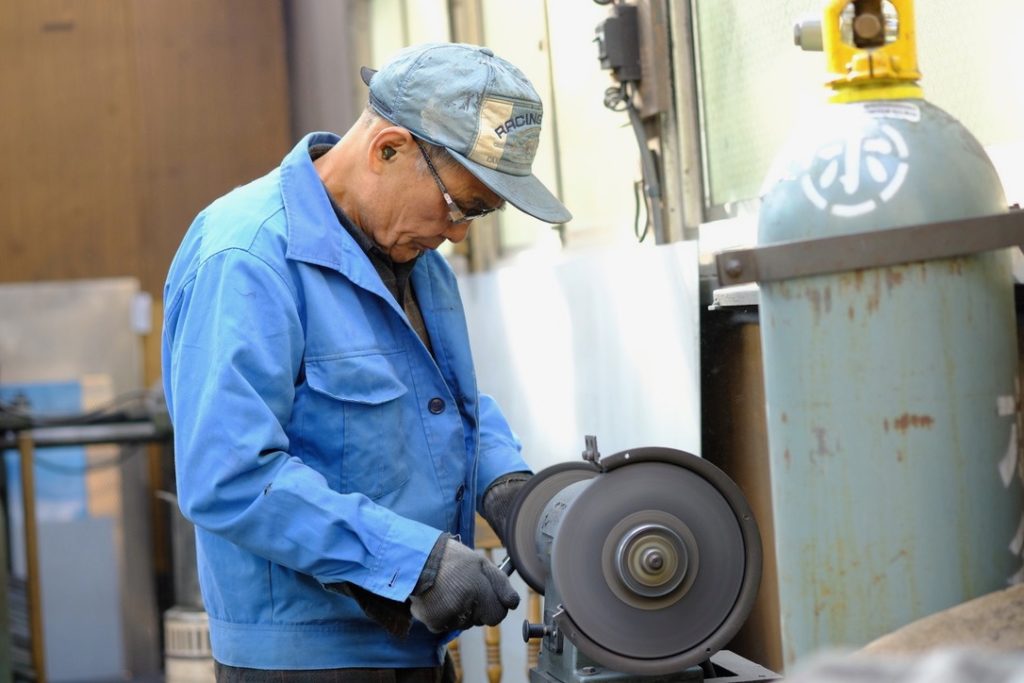
Buff polishing
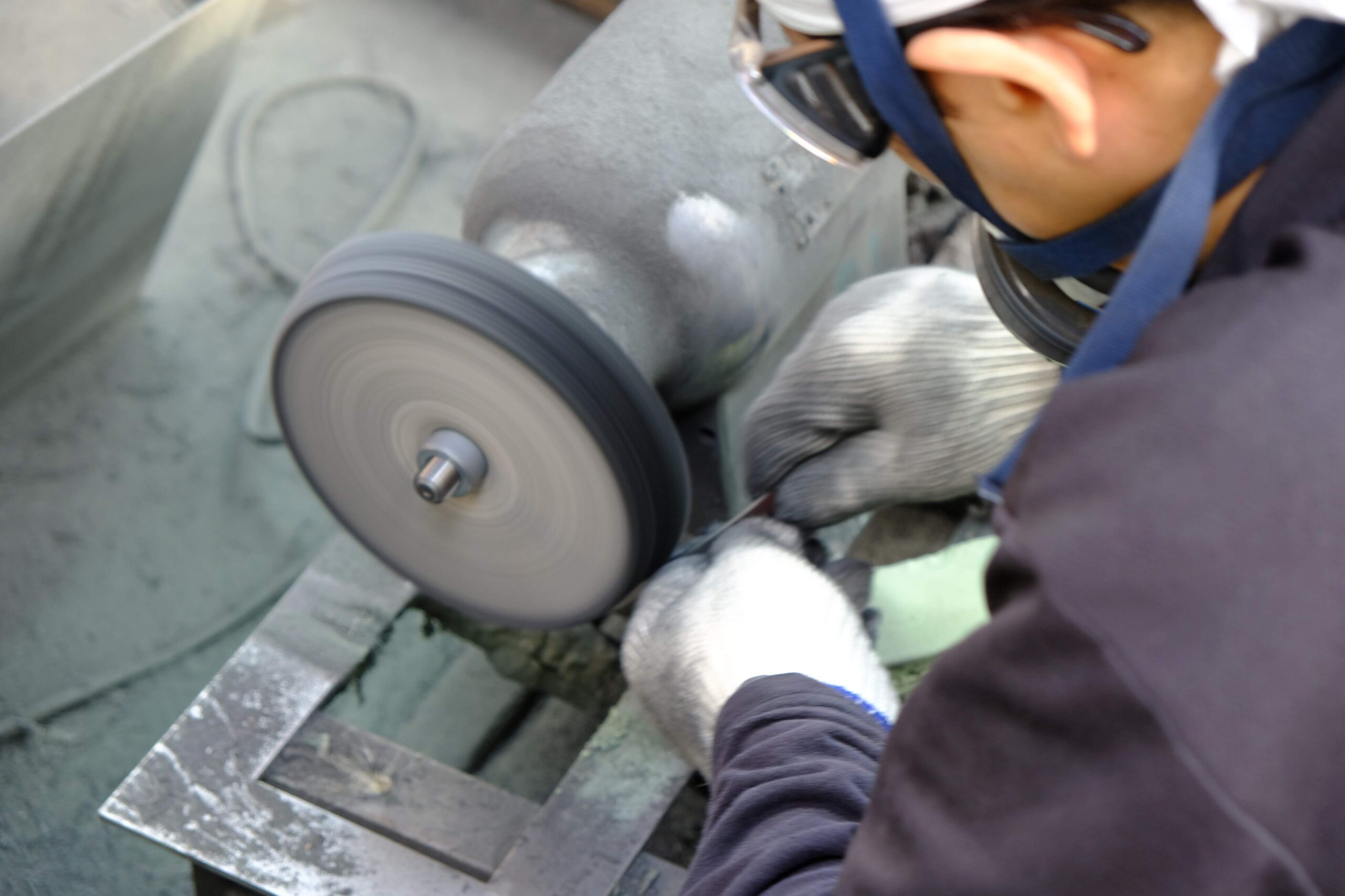
We perform a unique buffing process that is unique to our original business, which is a thin sheet metal shop.
Usually, sheet metal processing companies and polishing processing companies are completely different industries.
Polishing performed by sheet metal fabricators is limited to grinding off weld beads during the production process of sinks, frames, etc. with a grinder and then polishing them with a flexible polishing machine.
Hairline finish and #400 finish are standard specifications.
Polishing by polishing companies is a delicate process in which the surface is prepared in small increments using a fine-grit polishing cloth of #400 or higher.
At our company, we use a polishing method that takes advantage of the strengths of both, allowing us to efficiently and carefully polish mainly medical equipment and parts for food processing machinery.
Process
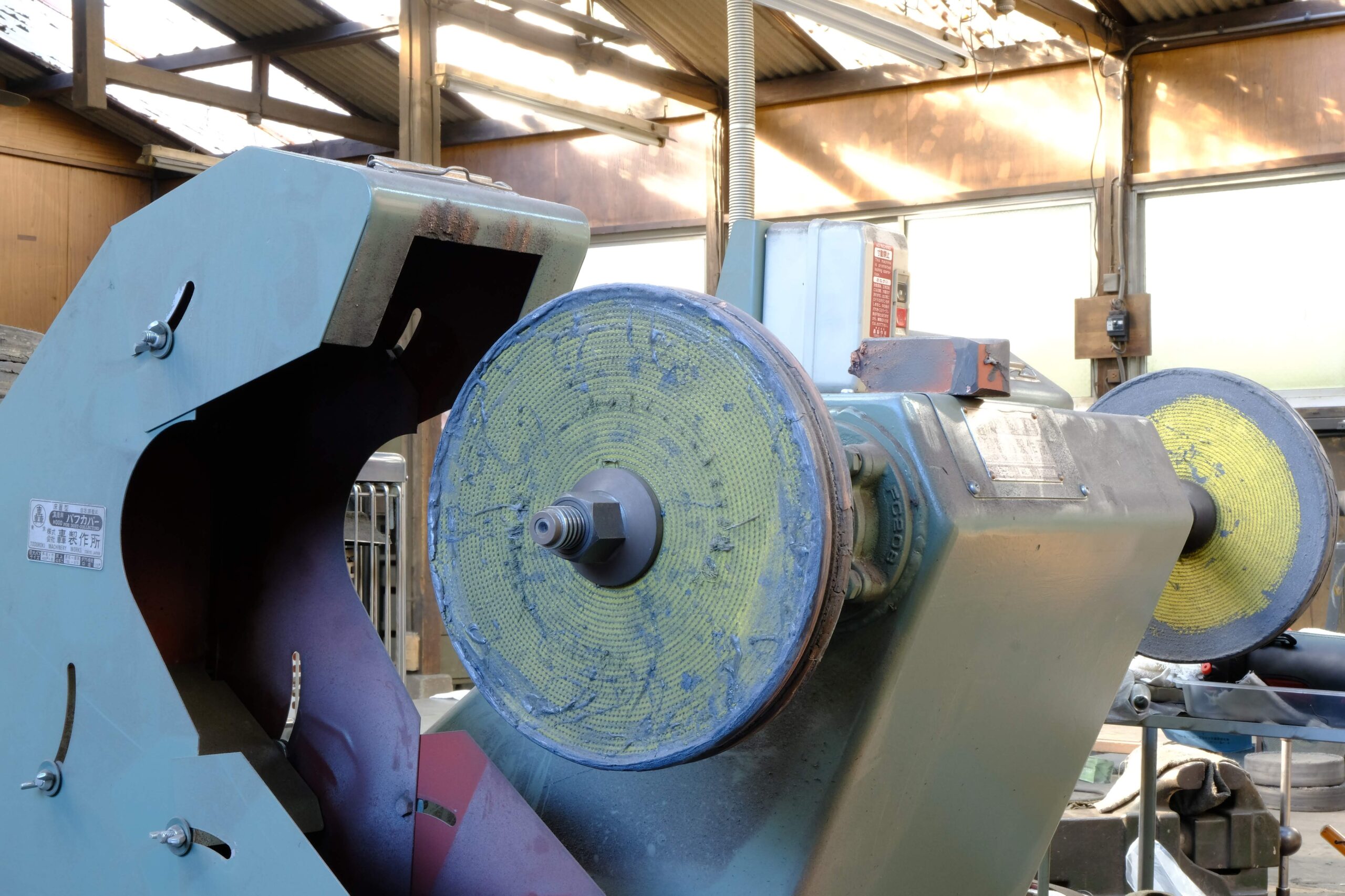
Step 1 Rough polishing
For rough polishing, we mainly use grinder-type tools, and polish while adjusting the shape with skill. This is the process that requires the most technical ability. It will be polished to approximately #150. Currently, there are extremely few polishing companies in Tokyo that can handle this rough polishing, but at our company, we have experienced workers in their 30s to 40s.
Step 2 Mid-finish polishing
Mid-finish polishing is a polishing process that uses a tool called an "iron buff." An iron buff is a cylindrical piece of cloth coated with abrasive powder and glue, and is also called an emery buff. By molding the fabric according to its shape, it is possible to polish it to suit various shapes. Semi-finish polishing using iron buffs is also an area in which the number of polishing companies that can handle this work is drastically decreasing in the suburbs of Tokyo. The finish will be approximately #250.
Step 3 Finish polishing
Final polishing is done using a sisal buff. Apply an abrasive to a sisal buff made of woven hemp and polish it. The finish will be about #400. For #400 and above, use flannel buffing or felt buffing to create a finer finish on the polished surface.
Hairline finish, satin finish, etc. are also available upon request.
Samples
Medical device
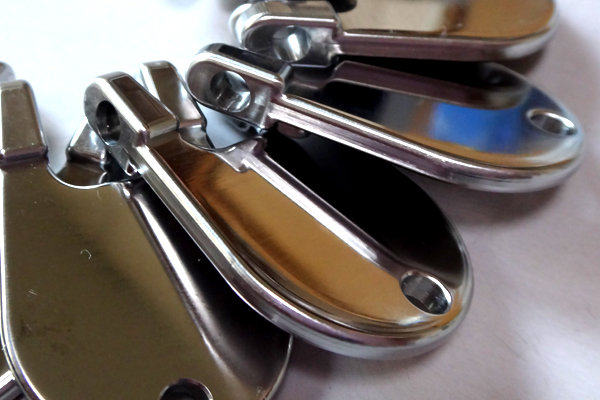
We undertake the polishing of medical instruments, mainly steel instruments (stainless steel and brass) called forceps. We perform rough polishing, semi-finishing, and final polishing based on the condition of the casting surface and machined grain, and perform polishing up to #400 while forming. Currently, we have a track record of about 300 units/month.
Food processor parts
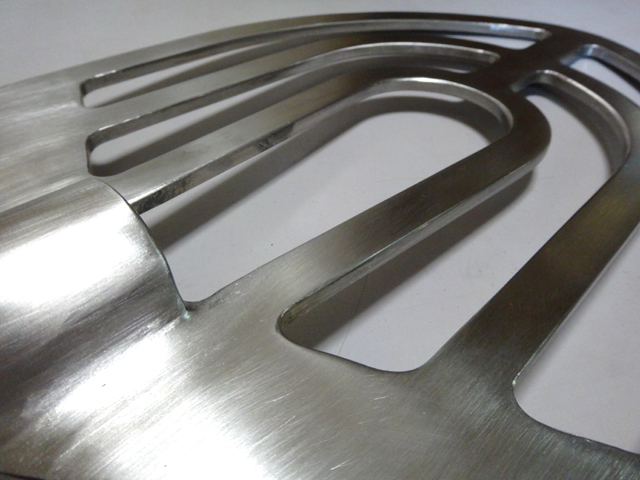
We polish and finish food machinery parts after welding. From bead cutting to semi-finishing and final polishing. Even if a welding defect occurs, we can immediately fill it in-house and repolish it, allowing us to respond quickly.
Medical device manufacturing/polishing
We use emery buffs and sisal buffs to polish medical instruments (such as steel instruments such as forceps) and food machinery parts.
Buffing of complex shapes with a wide variety of products in small quantities is one of the processing fields that requires the most craftsmanship.
At our company, we can handle everything from rough polishing of cast and forged materials to final polishing of #400.
Accurate polishing
At our company, precision polishing is also called lapping or hand polishing.
Buffing is a process in which polishing is performed using the rotational force of a buffing machine, whereas precision polishing uses a special abrasive material and is polished by hand according to the shape.
Compared to buffing, processing time is required, but fine polishing is possible. We support sizes from #300 to #1500 as standard. Mainly used for surface polishing of precision mechanical parts
In semiconductor manufacturing equipment and food/medical machine parts, machining cuts (cutter marks) can cause problems such as corrosion. Precision polishing technology can eliminate these cutting marks and prepare the surface without changing the dimensions.
Dimensional change less than 0.01mm
Depending on the surface roughness of the original part, the dimensional change will be less than 0.01mm. (If the original is about Ra1.6, it is about 2 to 3 μm)
The standard surface roughness is about Ra0.8, but it is possible to achieve a surface roughness of about Ra0.2 if the budget allows.
This is an advanced technique that only one person at our company can perform. We receive many requests not only for polishing precision parts, but also for polishing works of art and souvenirs.
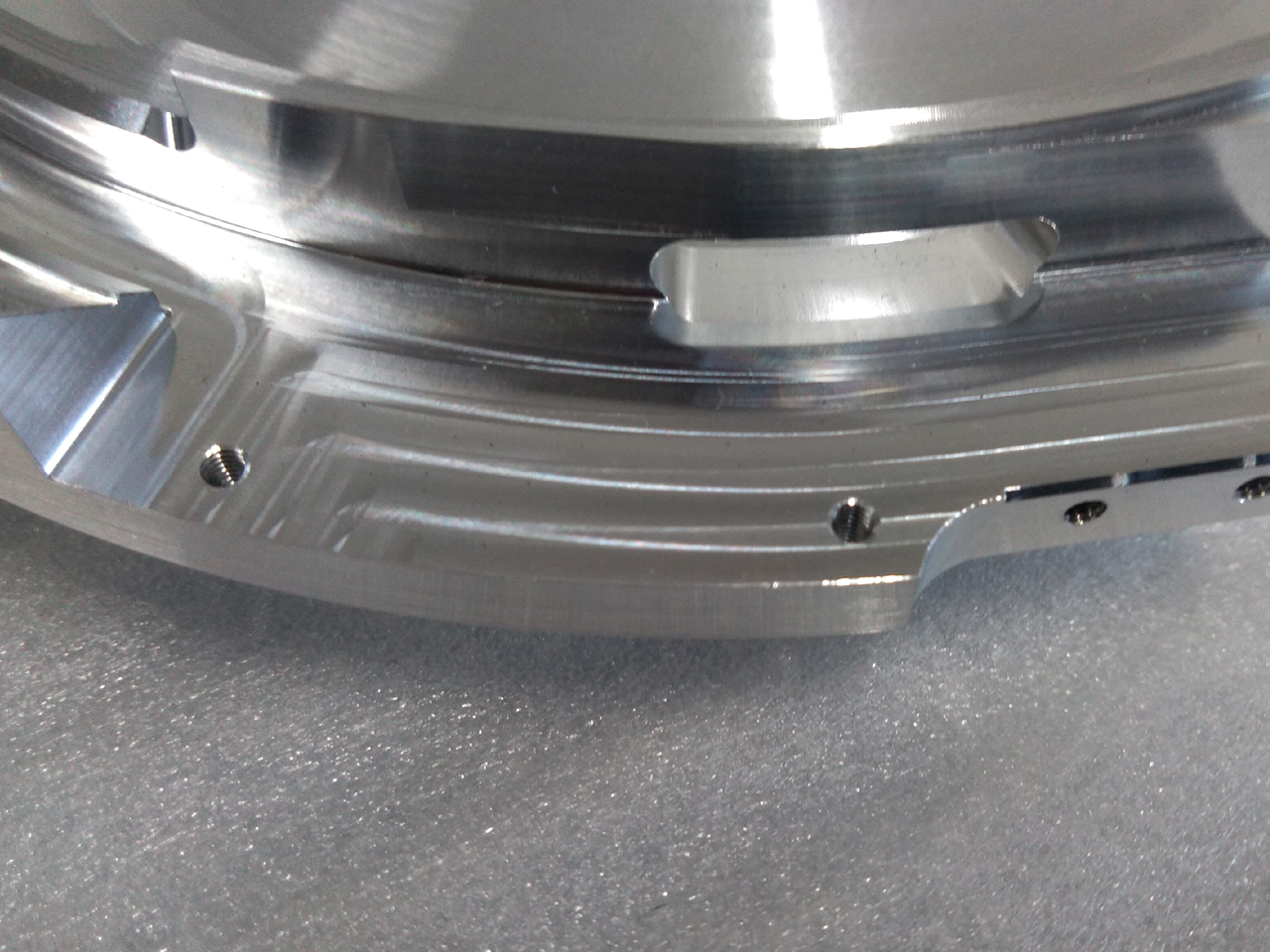
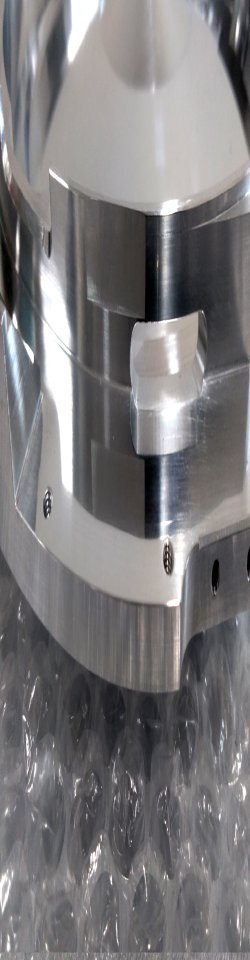
This is an example of actual wrapping. The left image is before accurate polishing, and the right image is after accurate polishing.
Before wrapping, cutter marks appear floating and the overall appearance is dull.
After accurate polishing, cutter marks are removed and the overall surface becomes glossy.
You can probably see the difference by clearly seeing the outline of the reflected shape.
The actual surface roughness is about Ra0.4~0.8μm.
Samples
Machined SEM parts
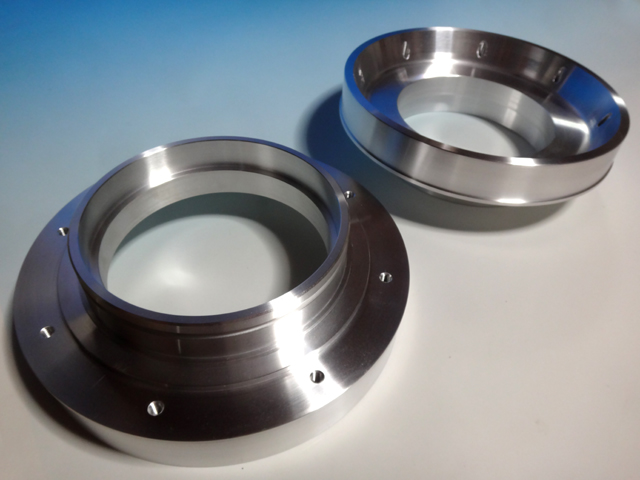
High-precision machined parts are finished to a quasi-mirror finish of approximately Ra0.4 without compromising dimensional accuracy.
Ornament
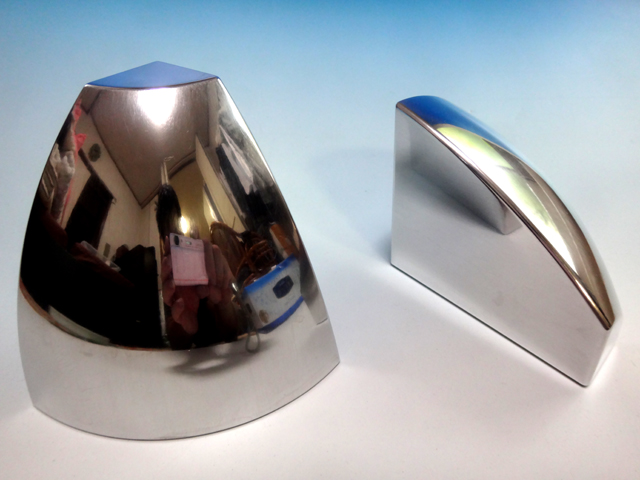
We performed surface polishing of aluminum parts with curved surfaces. If you use buffing, the corners will sag, which could ruin the shape of the cutting process. Hand polishing allows for a fine finish on easily scratched aluminum materials without causing any dimensional changes. Finished to a quasi-mirror finish of about Ra0.4.