What is milling?
Cutting is one of the main machining methods, along with lathe processing, in the production of mechanical parts.
Cutting is a process in which a rotary tool called an end mill is pressed against a material (workpiece) to cut it.
Machining using machine tools such as general-purpose milling cutters, NC milling cutters, and machining centers is typical.
It can be said to be an indispensable processing method for manufacturing precision parts.
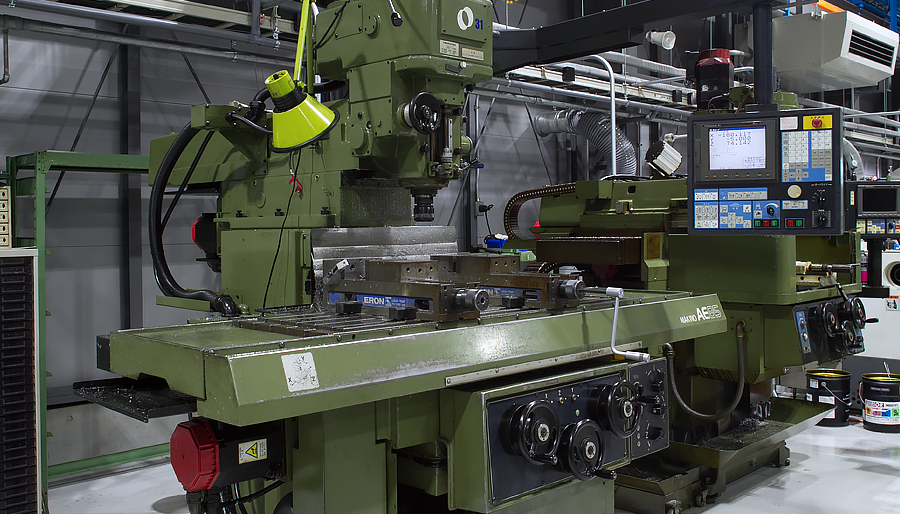
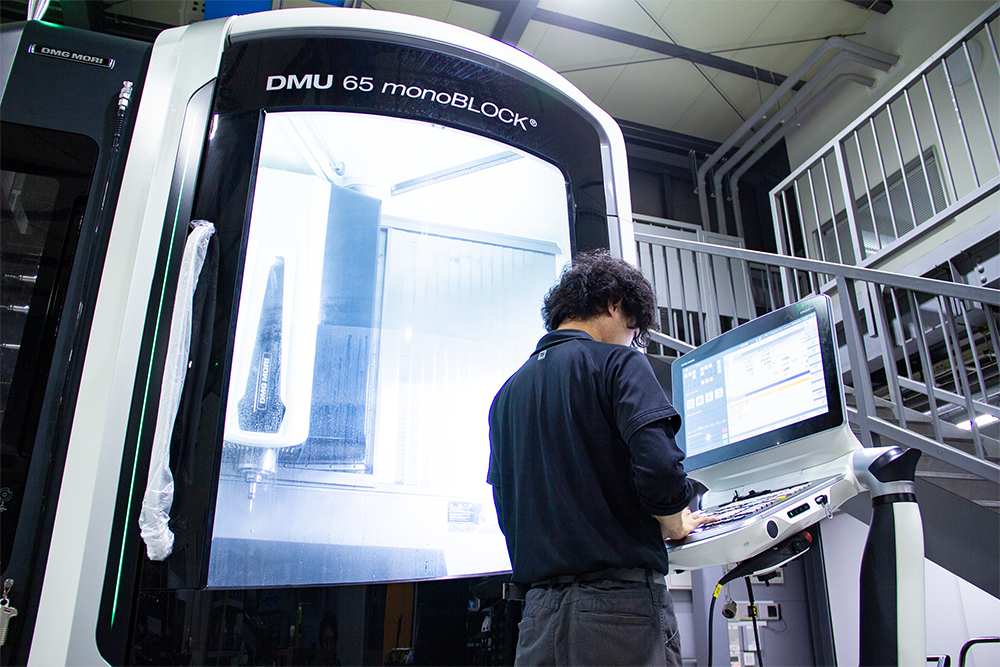
What is machining center?
A machining center is a typical machine tool used for milling-type cutting processing.
Precise machining is possible through NC control, and cutting can be performed automatically according to the NC program.
It is different from NC milling in that it has an ATC (Auto Tool Changer) function and can continue machining while automatically changing the end mill.
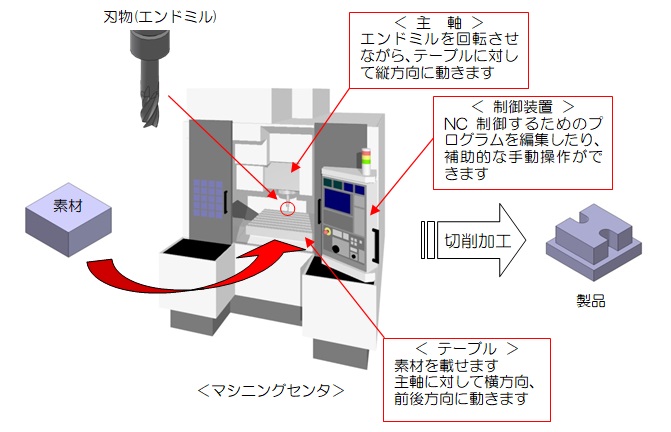
The diagram above shows the appearance of a typical machining center.
A machining center has a rotating and movable spindle with a cutting tool (end mill) attached to it for cutting the workpiece.
It has a table on which to place the workpiece, and is equipped with a control device for storing NC control programs and for manual operation.
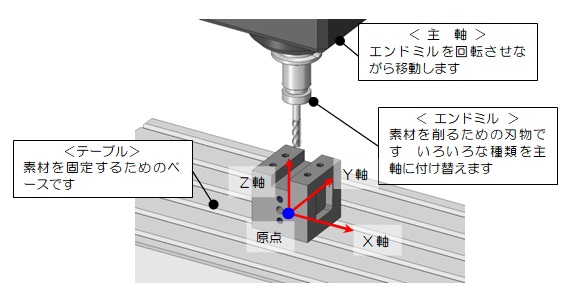
The inside of the machining center is shown in the diagram above.
A machining center has a main axis (or table) that can move freely in three axes: the X-axis (left and right), the Y-axis (back and forth), and the Z-axis (up and down) when facing the machine.
What you can do with milling
Milling is a process that creates a desired shape by removing unnecessary parts from a material.
We can produce parts of various shapes with high precision, from simple shapes such as holes and notches in a block shape to curved shapes and composite shapes.
Furthermore, by making full use of 5-axis machining, we are good at cutting complex shapes.
Simple shape
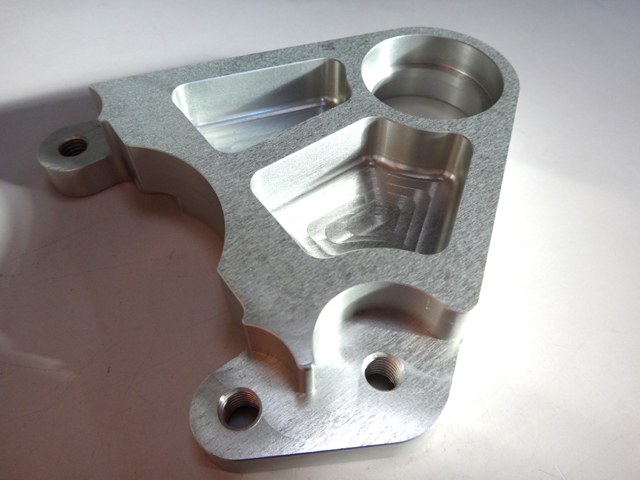
Composite shape
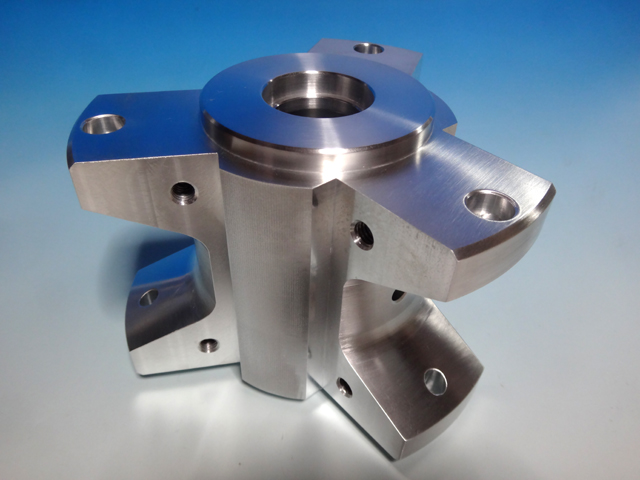
Free surface
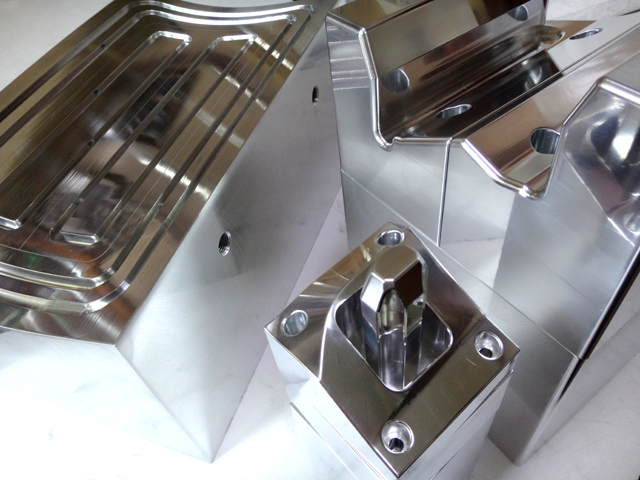
Complex shape
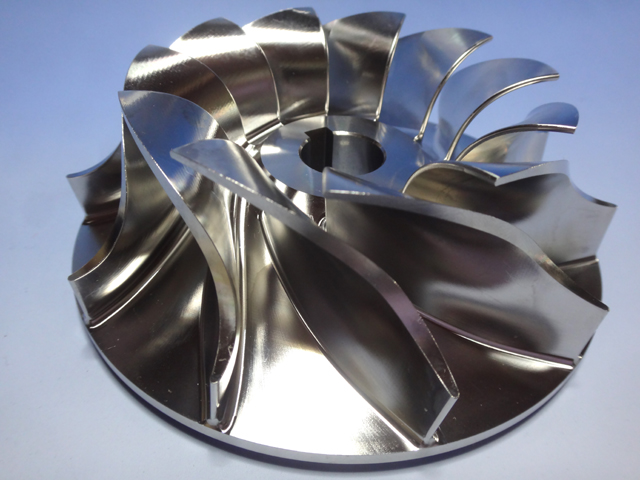
Process flow
Milling is performed with the surface to be machined directly facing the end mill.
If other surfaces need to be machined, release the fixation and machine the next surface directly facing the end mill.
Fixing the material on the table and preparing it for processing is called "setup."
Changing the direction from one setup to the next setup is called a "setup change."
Cutting process creates the desired shape by repeating "setup" → "processing" → "setup change" → "processing".
If you understand the flow of cutting, you may be able to find hints for designing parts.
Features and precautions
There are a wide variety of types of blades and processing methods used in cutting.
In addition, since a rotating tool is used for cutting, there is always a "corner radius" at the corners of the three sides.
If the shape is too deep, there are restrictions such as the overhang of the end mill being too long and machining impossible.
Regarding hole machining, it is also necessary to design with the presence of pilot holes in mind.
We have summarized the characteristics and precautions of cutting processing.
Difficult shape for milling
Cutting is a highly versatile processing method that can produce various shapes with high precision.
However, due to the principle of removal machining, there are some shapes that are difficult to cut, such as undercuts and thin shapes, so be careful.
3D shape
Cutting can process flat surfaces and cylindrical shapes with high precision, but it is also effective in machining three-dimensional shapes with inclined surfaces and free-form surfaces.
5-axis machining
Milling is a powerful tool that can process 3D free-form surfaces, but using the latest 5-axis processing machines expands the possibilities even further.
There are some parts, such as impellers and turbine blades, that can only be realized with simultaneous 5-axis machining.